Case Study: AI-Powered Label Detection for Beverage Bottle Inspection
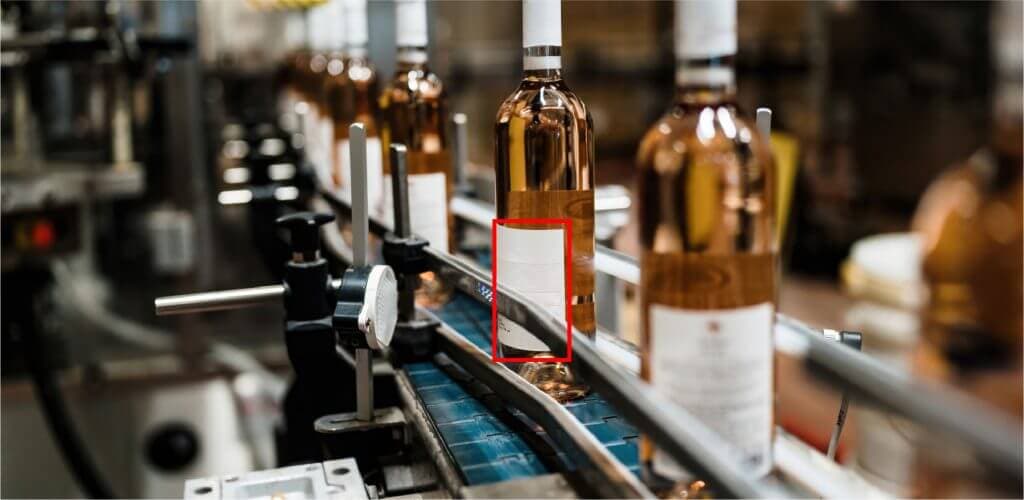
Client Profile
Industry: Beverage Manufacturing
Size: Mid-sized beverage company with multiple product lines
Location: United States
Production Volume: 120 million bottles annually
Our client is a growing beverage manufacturer producing a diverse range of products including soft drinks, flavored water, and specialty beverages. With multiple product lines and frequent changeovers, they faced significant challenges in maintaining consistent label quality across their high-speed bottling operations.
The Challenge
The Vision AI solution for bottle label inspection
Despite investments in modern bottling equipment, the client was experiencing persistent challenges with their label inspection process:
- Manual Inspection Limitations: Quality control staff could only inspect a small percentage of bottles, missing many defects.
- High-Speed Production: Production lines running at 600 bottles per minute made visual inspection extremely difficult.
- Multiple Label Types: Different products required different labels, increasing complexity during changeovers.
- Curved Surface Challenges: The cylindrical bottle surface created unique challenges for label application and inspection.
- Costly Recalls: Mislabeled products occasionally reached retailers, resulting in expensive recalls and brand damage.
- Regulatory Compliance: Strict FDA requirements for accurate labeling created additional pressure for perfect execution.
Misaligned labels on a bottle
The Operations Director explained their situation: "Label issues were our number one quality problem. Missing labels, misaligned applications, wrinkled surfaces, and smudged printing were all occurring at various rates. Our manual inspection process simply couldn't keep pace with our production speed, and we were spending too much on rework and recalls."
The Solution
After evaluating several options, the company partnered with Visionify to implement a comprehensive Machine Vision Label Inspection System across their bottling lines:
The Vision AI solution for bottle label inspection
1. Automated Inspection System
- Installation of high-speed line scan cameras at critical inspection points
- Custom lighting setup (vision bar) optimized for curved bottle surfaces
- Encoder wheel integration for precise line synchronization
- Real-time image capture and analysis of each bottle during production
2. Advanced Defect Detection
- Computer vision algorithms specifically trained to identify multiple label issues:
- Missing labels
- Misalignment and skewed application
- Wrinkles and bubbles
- Print quality issues (smudging, fading, incorrect colors)
- Barcode and date code verification
- Machine learning models capable of adapting to different label types and bottle shapes
3. Intelligent Rejection System
- Real-time defect classification by type and severity
- Automated rejection mechanism for defective bottles
- Customizable rejection thresholds based on defect type
- Minimal production disruption during rejection process
4. Quality Analytics Platform
- Comprehensive reporting on defect types, frequencies, and trends
- Production line performance metrics
- Batch-specific quality statistics
- Early warning system for emerging quality issues
Implementation Process
The Vision AI solution for bottle label inspection
The implementation followed a structured approach to ensure minimal disruption to production:
-
Assessment & Planning (3 weeks)
- Comprehensive analysis of current bottling and labeling processes
- Identification of optimal inspection points in the production line
- Camera and lighting placement planning
- Development of integration strategy with existing systems
-
Pilot Deployment (4 weeks)
- Installation on one bottling line
- Initial model training with thousands of bottle images
- Calibration of detection thresholds and classification parameters
- Side-by-side comparison with manual inspection results
-
Model Refinement (3 weeks)
- Analysis of false positives and false negatives
- Additional training to improve detection accuracy
- Fine-tuning of classification thresholds to optimize rejection rates
- Validation against expert human inspectors
-
Full-Scale Implementation (8 weeks)
- Phased rollout across all bottling lines
- Integration with production management systems
- Comprehensive training for quality control and production staff
- Development of standard operating procedures
-
Continuous Improvement (Ongoing)
- Regular model updates based on new label designs
- Periodic retraining with new production data
- System optimization for different bottle types and label materials
- Addition of new detection capabilities as needed
Results
After six months of operation, the Machine Vision Label Inspection System delivered significant improvements across multiple performance metrics:
Quality Improvements
- 99.2% reduction in mislabeled products reaching the market
- 100% inspection coverage of all bottles produced
- Detection accuracy of 99.8% for critical label defects
- Zero product recalls due to labeling issues since implementation
- Consistent quality standards across all product lines and production shifts
Operational Efficiencies
- 34% increase in production throughput
- Inspection capacity matching production speed of 600 bottles per minute
- 72% reduction in quality control labor costs
- 24/7 operation without inspection fatigue or variability
- Real-time quality feedback to production teams
Financial Impact
- Annual savings of $380,000 in reduced recalls and rework
- $210,000 decrease in labor costs
- Increased revenue from higher production throughput
- ROI of 275% within the first year
- Payback period of 4.4 months
Additional Benefits
- Regulatory Compliance: Ensured adherence to FDA labeling requirements
- Enhanced Brand Reputation: Elimination of mislabeled products reaching consumers
- Data-Driven Insights: Identification of patterns in defects led to upstream process improvements
- Better Resource Allocation: Quality control staff focused on process improvement rather than routine inspection
- Reduced Waste: Fewer rejected products and materials due to early detection of issues
Key Success Factors
Several elements were crucial to the project's success:
-
Specialized Imaging Techniques: Line scan technology optimized for cylindrical surfaces.
-
Synchronized Inspection: Encoder wheel integration ensured precise timing with production line speed.
-
Customized Lighting: Vision bar illumination designed specifically for label materials and bottle surfaces.
-
Adaptive Algorithms: Machine learning models that could adjust to different label designs and bottle types.
-
Minimal Disruption: Implementation approach that maintained production continuity.
Implementation Challenges & Solutions
The project faced several challenges during implementation:
-
Curved Surface Inspection
- Challenge: Cylindrical bottle surfaces created distortion in label images
- Solution: Development of specialized algorithms to compensate for curvature and ensure accurate defect detection
-
Production Speed
- Challenge: High-speed bottling lines required ultra-fast image capture and processing
- Solution: Implementation of line scan cameras and parallel processing architecture to match production pace
-
Label Variety
- Challenge: Frequent changeovers between different products and label designs
- Solution: Creation of a flexible system with rapid reconfiguration capabilities and automatic recognition of label types
-
Environmental Factors
- Challenge: Wet conditions and condensation on bottles affected image quality
- Solution: Environmental controls and specialized lighting to minimize interference from moisture
Client Testimonial
"Visionify's label inspection system has completely transformed our quality control process. We're now able to inspect every single bottle with a level of accuracy that was impossible with manual inspection. The system has eliminated labeling-related recalls entirely, which has saved us hundreds of thousands of dollars and protected our brand reputation. The insights we've gained from the analytics have also helped us improve our upstream processes, making our entire operation more efficient."
— Sarah T., Director of Operations
Machine Vision Technology Overview
Our solution leverages several advanced technologies to provide accurate, high-speed label inspection:
Specialized Imaging System
- High-resolution line scan cameras capture detailed images of each bottle as it rotates
- Custom vision bar lighting system to highlight label defects
- Multiple imaging angles to ensure comprehensive coverage
- Encoder wheel integration for precise synchronization with line speed
Advanced Detection Algorithms
- Custom computer vision algorithms trained specifically for label defect patterns
- Deep learning models that can distinguish between actual defects and normal variations
- Optical character recognition (OCR) for verifying text elements
- Barcode verification to ensure scannable products
Real-Time Processing
- Edge computing architecture for immediate analysis at the production line
- Parallel processing to handle high-volume image data
- Low-latency decision making for timely rejection of defective bottles
- Continuous learning capability to improve detection over time
Analytics and Reporting
- Comprehensive tracking of defect statistics by product, shift, and production line
- Trend analysis to identify recurring issues
- Early warning system for emerging problems
- Integration with enterprise quality management systems
Visionify – Empowering Beverage Quality Through Vision AI
Our Machine Vision Label Inspection solution provided our client with powerful tools to overcome their label quality challenges. Through automated detection, intelligent classification, and comprehensive analytics, Visionify not only helped eliminate mislabeled products but also enhanced production efficiency and regulatory compliance.
Our client can now confidently distribute their beverage products knowing that virtually all labeling issues are detected before bottles leave the facility. This successful implementation exemplifies how Visionify's innovative computer vision solutions can transform beverage manufacturing quality control through advanced AI technology.
Conclusion
This case study demonstrates how machine vision technology can revolutionize label inspection in the beverage industry. By implementing an AI-powered inspection system, our client was able to significantly reduce labeling defects while improving production efficiency and eliminating costly recalls.
The success of this implementation has led to the company exploring additional applications of computer vision technology in their manufacturing processes, including cap inspection and fill-level verification. The data collected from the system has also provided valuable insights for process improvements that have further enhanced product quality and production efficiency.
Are you facing similar labeling challenges in your beverage manufacturing operations? Contact Visionify today to learn how our Machine Vision solutions can transform your approach to product quality and production efficiency.
Ready to achieve similar results?
Let us show you how our Vision AI safety solutions can transform your workplace safety.
Schedule a ConsultationRelated Case Studies

Case Study: How Indorama Ventures Transformed Workplace Safety at Their Panipat Plant with Visionify's AI Solutions
Manufacturing
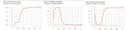
Case Study: How a Leading Irrigation Equipment Manufacturer Enhanced Drilling Precision with Visionify's AI Quality Check Solution
Manufacturing
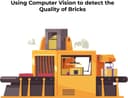
Case Study: Using Computer Vision to Detect the Quality of Bricks
Manufacturing
Schedule a Meeting
Book a personalized demo with our product specialists to see how our AI safety solutions can work for your business.
Choose a convenient time
Select from available slots in your timezone
30-minute consultation
Brief but comprehensive overview of our solutions
Meet our product experts
Get answers to your specific questions