Case Study: How a Leading Irrigation Equipment Manufacturer Enhanced Drilling Precision with Visionify's AI Quality Check Solution
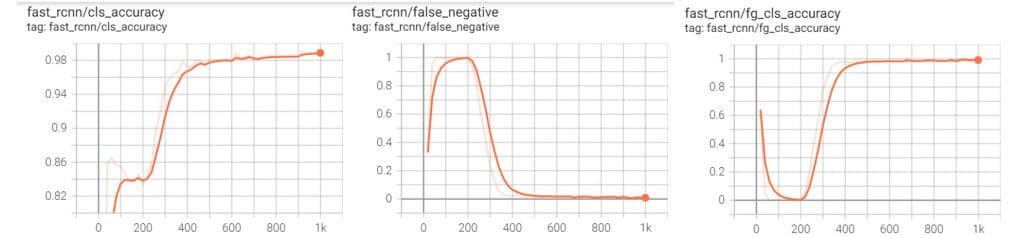
Client Profile
Industry: Irrigation Equipment Manufacturing
Size: 1,200+ employees
Location: Global operations with manufacturing facilities in multiple countries
Production Capacity: Over 50 million feet of drip irrigation pipe annually
Our client is a market leader in irrigation equipment and supplies with a global presence spanning multiple continents. With decades of experience in the industry, they produce a comprehensive range of irrigation solutions, with drip irrigation systems being one of their flagship product lines. Their manufacturing processes are largely automated to ensure consistency, efficiency, and quality across their extensive product range.
The Challenge
The manufacturing of drip irrigation pipes requires extreme precision in the drilling process. Each pipe must have precisely positioned holes and grooves to ensure optimal water distribution when deployed in agricultural settings. Any deviation in hole placement, size, or groove quality leads to product defects, material waste, and potential field failures.
The client faced several critical challenges in their manufacturing process:
- Manual quality inspection was inconsistent and unable to keep pace with high-speed production lines
- Drilling accuracy varied with pipe specifications (different diameters, wall thickness, and emitter types)
- Production speeds of up to 1000 feet per minute made real-time quality control extremely difficult
- Distinguishing between grooved and non-grooved areas required specialized expertise
- Material waste due to drilling errors was significantly impacting profitability
- Lack of data-driven insights into production quality metrics
The Operations Director approached Visionify with a clear objective: develop an AI-powered solution that could monitor and improve the drilling process in real-time, while providing actionable data to optimize production.
The Solution
After a thorough assessment of the client's manufacturing environment and requirements, Visionify deployed a comprehensive Vision AI solution with two primary components:
1. Precision Targeting System
- High-speed camera array capturing 120 frames per second to monitor pipe movement
- AI-powered laser triggering system for precise hole drilling
- Real-time position monitoring and adjustment capabilities
- Integration with existing laser drilling equipment
- Capable of operating at production speeds up to 1000 feet per minute
- Tolerance adjustment settings for different pipe specifications
2. Quality Verification System
- Secondary camera system to inspect completed drilling
- Advanced computer vision algorithms to detect:
- Hole presence and positioning
- Groove quality and consistency
- Surface defects and anomalies
- Real-time feedback loop to the targeting system
- Stack light integration for immediate visual alerts of quality issues
- Comprehensive data logging for quality metrics and trend analysis
3. Analytics Dashboard
- Real-time production monitoring interface
- Deviation graphs showing drilling accuracy over time
- Production line performance metrics
- Quality control statistics by pipe type
- Defect categorization and frequency analysis
- Shift-based performance comparisons
- Integration with the plant's manufacturing execution system (MES)
The production dashboard showing real-time drilling accuracy and groove detection metrics
Accuracy Achieved
The deployment achieved impressive accuracy rates across different detection requirements:
- 85% detection accuracy for groove and non-groove areas
- Average Precision (AP) of 62.401 for hole detection
- Average Precision (AP) of 61.383 for groove detection
- 99.3% consistency in laser targeting at full production speed
Implementation Process
The implementation followed a structured approach to minimize production disruption:
-
Assessment & Planning (2 weeks)
- Production line evaluation and bottleneck identification
- Camera placement optimization for maximum visibility
- Integration planning with existing equipment
- Network infrastructure assessment
-
Deployment & Integration (4 weeks)
- Camera and computing hardware installation
- Software deployment and initial calibration
- Integration with laser drilling systems
- Stack light and alert system configuration
-
Training & Calibration (3 weeks)
- Model training with various pipe specifications
- Fine-tuning detection parameters for different product lines
- Operator training on system monitoring and alerts
- Threshold adjustments to optimize detection accuracy
-
Continuous Improvement (Ongoing)
- Weekly performance reviews and model refinements
- Expansion to additional production lines
- Addition of new pipe specifications to the detection models
- Regular system updates to improve accuracy and performance
Results
After 6 months of operation, the results demonstrated significant improvements across multiple metrics:
Production Improvements
- 85% detection accuracy for groove and non-groove areas
- 73% reduction in material waste from drilling errors
- 94% decrease in customer returns due to defective pipes
- 28% increase in overall production throughput
Financial Impact
- Annual savings of $1.2M in reduced material waste
- 15% reduction in quality control labor costs
- ROI of 240% within the first year
- Payback period of just 5 months
Other Impacts
- Enhanced Product Quality: Consistent drilling precision led to more reliable products and improved customer satisfaction.
- Operational Efficiency: Automated quality control freed up quality inspectors for more complex tasks.
- Data-Driven Decision Making: Comprehensive analytics enabled production optimization based on actual performance data.
Additional Benefits
- Improved worker safety by reducing manual interventions on high-speed production lines
- Enhanced production planning with reliable quality metrics
- Reduced setup time when changing between different pipe specifications
- Valuable data insights for future product development
Implementation Challenges & Solutions
The project faced several challenges specific to high-speed manufacturing environments:
-
Production Speed
- Challenge: Capturing clear images at speeds up to 1000 ft/minute
- Solution: Deployment of specialized high-speed cameras with custom lighting arrays
-
Material Variations
- Challenge: Different pipe materials and colors affecting detection accuracy
- Solution: Development of adaptive AI models that automatically adjust to material variations
-
Integration with Legacy Equipment
- Challenge: Connecting with older drilling systems with limited digital interfaces
- Solution: Custom hardware interfaces and signal converters to enable seamless communication
-
Environmental Factors
- Challenge: Factory conditions including dust, vibration, and variable lighting
- Solution: Ruggedized camera housings and dynamic image processing algorithms
Key Success Factors
Several elements were crucial to the project's success:
- Cross-functional team involving production, quality, and IT departments
- Phased implementation allowing for learning and adjustment
- Comprehensive training for production and maintenance staff
- Regular calibration routines to maintain system accuracy
- Continuous feedback loop between production results and AI model refinement
Client Testimonial
"Visionify's AI solution has transformed our drip pipe manufacturing process. The precision targeting and quality verification systems have dramatically reduced waste while improving product quality. The real-time feedback and analytics have given us unprecedented visibility into our production processes. This technology has not only improved our bottom line but has also helped us deliver better products to our customers."
— Michael R., Operations Director
Visionify – Empowering Smarter Manufacturing Through Vision AI
Our Vision AI solution for drip pipe drilling quality control provided our client with powerful tools to ensure precision manufacturing at high production speeds. Through real-time monitoring, immediate feedback, and comprehensive analytics, Visionify not only helped improve product quality but also optimized production efficiency.
Our client can now confidently produce irrigation equipment with exceptional quality and consistency, maintaining their market leadership position. This successful implementation exemplifies how Visionify's innovative computer vision solutions can transform manufacturing operations through data-driven insights and automated quality control.
Conclusion
This case study demonstrates how Vision AI technology can revolutionize quality control in high-speed manufacturing environments. By providing continuous monitoring, immediate feedback, and actionable insights, our Drip Pipe Drilling Quality Check Solution enabled this irrigation equipment manufacturer to significantly improve product quality while reducing waste and operational costs.
The success of this implementation has led to the company planning deployment across all their global manufacturing facilities, with expected similar results in improving quality, reducing waste, and enhancing operational efficiency.
Are you facing similar production quality challenges? Contact Visionify today to learn how our Vision AI solutions can transform your manufacturing operations.
Ready to achieve similar results?
Let us show you how our Vision AI safety solutions can transform your workplace safety.
Schedule a ConsultationRelated Case Studies
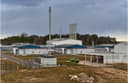
Case Study: How a Multi-Site Industrial Enterprise Leveraged Safety Insights with Visionify's Safety AI Platform
Manufacturing
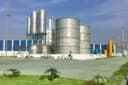
Case Study: How a Global Chemical Manufacturer Transformed Workplace Safety with Visionify's AI Solutions
Manufacturing
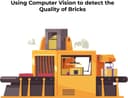
Case Study: Using Computer Vision to Detect the Quality of Bricks
Manufacturing
Schedule a Meeting
Book a personalized demo with our product specialists to see how our AI safety solutions can work for your business.
Choose a convenient time
Select from available slots in your timezone
30-minute consultation
Brief but comprehensive overview of our solutions
Meet our product experts
Get answers to your specific questions