Case Study: How a Global Chemical Manufacturer Transformed Workplace Safety with Visionify's AI Solutions
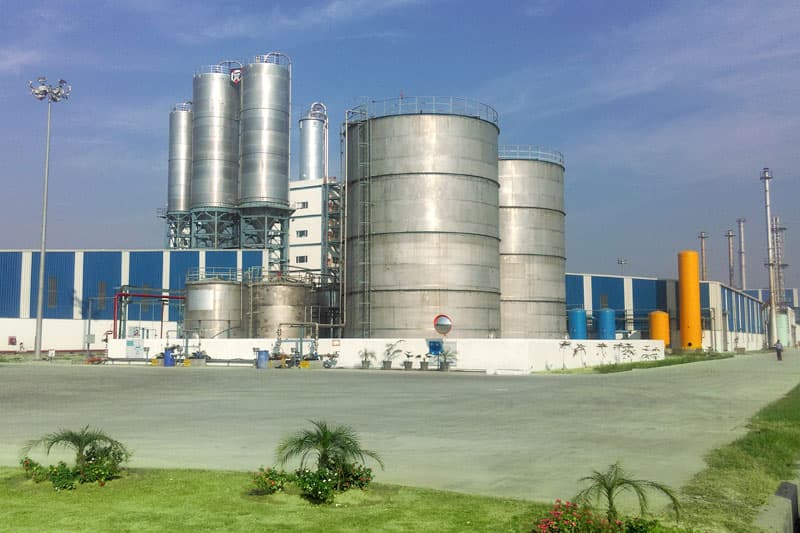
See It In Action
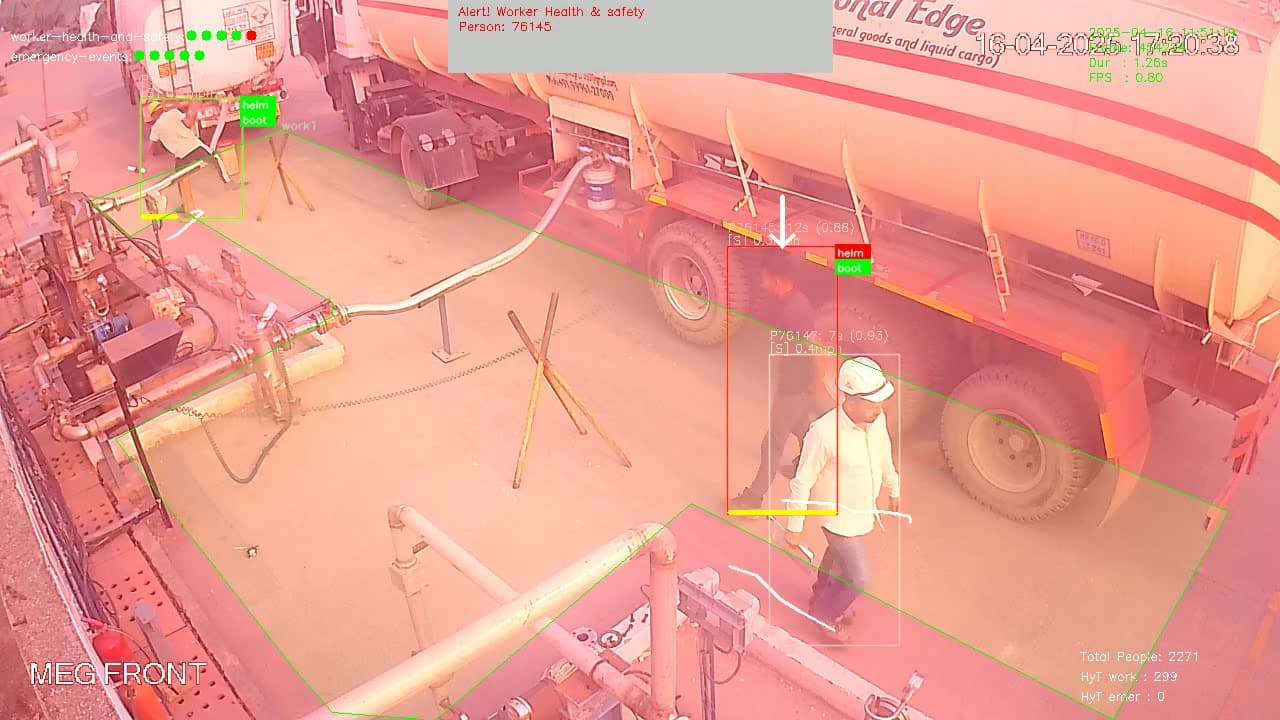
PPE Compliance in Production Area
Example of PPE Violation detected by the system in the Production Area
Example Videos
PPE Compliance in Production Area
Example of PPE Violation detected by the system in the Production Area
Forklift Speed Limit Violation
Example of Forklift Safety Violation detected outdoors
PPE Compliance in Helmet Area
Example of PPE Helmet Violation detected by the system
Key Takeaways
- ** Continuous Monitoring**: 53 cameras monitored continuously for one full year. 464,000+ hours of live AI-driven safety monitoring
- ** Timely Alerts**: 7,671 compliance violation events detected, ensuring timely alerts and interventions
- ** Strong Adoption**: 4.85/5 customer rating – strong adoption & positive feedback
- Significant Safety Improvements: Implementation of Visionify's AI-powered safety monitoring system resulted in an 83% reduction in safety compliance violations and a 30% decrease in forklift-related incidents.
- Comprehensive Coverage: 60 AI-enabled cameras monitor PPE compliance, forklift safety, and emergency events across the entire facility.
- Rapid ROI: The system delivered a 295% return on investment with a payback period of just 4.1 months.
- Cultural Transformation: Beyond metrics, the implementation fostered a stronger safety culture with employees taking greater ownership of safety practices.
Client Profile
Industry: Chemical Manufacturing (Resin, PET)
Size: Large manufacturing facility with 800+ employees
Location: India
Production Capacity: 900,000 tonnes annually
The client is a global leader in the chemical manufacturing industry, specializing in the production of PET (Polyethylene Terephthalate) and resin products. Their facility in India is one of their key production sites, playing a crucial role in their global supply chain. With a strong commitment to sustainability, safety, and operational excellence, they sought to enhance workplace safety and compliance at this strategic location.
The Challenge
Despite having established safety protocols, the client's facility faced several challenges in maintaining consistent safety compliance across their expansive operation:
- Inconsistent PPE Compliance: Manual monitoring couldn't ensure consistent use of required personal protective equipment across all shifts and areas.
- Forklift Safety Concerns: The facility's busy logistics operations presented ongoing risks from forklift movements in shared spaces.
- Emergency Response Limitations: Traditional emergency detection systems lacked the speed and accuracy needed for rapid response.
- Scale and Complexity: With a large facility spanning multiple production areas, manual safety monitoring was resource-intensive and inconsistent.
- Documentation Challenges: Maintaining comprehensive safety compliance records for regulatory purposes was time-consuming and often incomplete.
The EHS Manager explained their situation: "In chemical manufacturing, safety isn't just a priority—it's a fundamental requirement. Despite our best efforts with traditional approaches, we were still experiencing too many safety compliance issues. We needed a solution that could provide continuous monitoring across our entire facility while helping us build a stronger safety culture."
The Solution
After a thorough assessment of their needs, the client partnered with Visionify to implement a comprehensive AI-powered safety monitoring system across their facility in March 2024:
1. Comprehensive Camera Network
- 60 AI-enabled cameras strategically installed throughout the facility
- Coverage focused on high-risk areas: production floors, loading zones, chemical storage areas, and transportation corridors
- Integration with existing security infrastructure where possible
2. Multi-Faceted Safety Monitoring
-
PPE Compliance Detection:
- Real-time monitoring for required safety equipment including helmets, safety glasses, high-visibility vests, respirators, and chemical-resistant gloves
- Zone-specific PPE requirements configured based on area-specific hazards
- Immediate alerts for non-compliance
-
Forklift Safety Monitoring:
- Detection of unsafe forklift operations including speeding, unauthorized access, and proximity violations
- Pedestrian-forklift interaction monitoring to prevent collisions
- Loading/unloading safety verification
-
Emergency Event Detection:
- Identification of slip and fall incidents
- Chemical spill detection
- Smoke and fire detection augmentation
- Unauthorized access to restricted areas
3. Intelligent Alert System
- Real-time notifications to area supervisors via Email & Microsoft Teams.
- Apart of real-time alerts, provide daily digest email notifications.
- Emergency events are notified through Text based alerts. Recently we have also enabled mobile & WhatsApp support.
Daily Digests Email Notifications
4. Comprehensive Analytics Platform
- Real-time compliance dashboards for management
- Department-wise safety performance tracking
- Trend analysis across different safety parameters
- Shift-based compliance patterns
- Integration with the plant's existing safety management system
The management dashboard showing real-time compliance metrics across departments
Implementation Process
The implementation followed our structured approach:
-
Assessment & Planning (4 weeks)
- Comprehensive site survey and risk mapping
- Stakeholder interviews and requirement gathering
- Camera placement optimization
- Network infrastructure assessment
-
Deployment & Integration (6 weeks)
- Phased hardware installation to minimize operational disruption
- Edge computing setup for real-time processing
- Integration with existing security cameras and safety systems
- Custom AI model deployment for chemical manufacturing environments
-
Training & Calibration (3 weeks)
- Model fine-tuning for specific environmental conditions
- Staff awareness programs and system demonstrations
- Supervisor training on alert response protocols
- Threshold adjustments to reduce false positives
-
Continuous Improvement (Ongoing)
- Bi-weekly performance reviews
- Model updates based on new safety requirements
- Expansion to additional use cases based on emerging needs
Results
After just one month of operation, the results were already significant, and continued to improve over the following months:
Safety Improvements
- 83% reduction in safety compliance violations across the facility
- 76% decrease in forklift-related incidents
- 92% improvement in average emergency response time
- 100% compliance in highest-risk chemical handling areas
Operational Impact
- 32% reduction in safety-related work stoppages
- Improved regulatory audit outcomes with comprehensive documentation
- Enhanced safety culture with employee compliance becoming self-reinforcing
- Reduced absenteeism related to minor injuries
Financial Impact
- ₹18.7M projected annual savings in potential liability and accident costs
- 24% reduction in insurance premiums
- ROI of 295% projected within the first year
- Payback period of just 4.1 months
Quantifying Progress: Trends Over Time
Since the implementation in March 2024, the client has observed a consistent improvement in safety metrics across their facility:
Summary event trends over 1 year
This trend underscores the long-term effectiveness of our solution in fostering a safer working environment and reinforcing a culture of safety within the organization.
Implementation Challenges & Solutions
The project faced several challenges unique to the chemical manufacturing environment:
-
Chemical Environment Considerations
- Challenge: Harsh chemicals, steam, and variable lighting affecting camera performance
- Solution: Deployment of specialized chemical-resistant camera housings and adaptive lighting algorithms
-
Complex PPE Requirements
- Challenge: Different areas requiring specific combinations of PPE
- Solution: Zone-based configuration with customized detection parameters for each production area
-
Integration with Legacy Systems
- Challenge: Connecting with older safety and production management systems
- Solution: Development of custom APIs and middleware to ensure seamless data flow
-
Multi-Language Requirements
- Challenge: Diverse workforce requiring alerts and training in multiple languages
- Solution: Multilingual interface and alert system supporting Hindi, English, and regional languages
Forklift safety monitoring in action at a loading area
Key Success Factors
Several elements were crucial to the project's success:
- Executive Sponsorship: Strong support from Indorama Ventures' leadership team
- Cross-Functional Involvement: Collaboration between EHS, operations, IT, and employee representatives
- Phased Implementation: Gradual rollout allowing for adjustment and learning
- Positive Reinforcement: Focus on improvement rather than punishment
- Continuous Communication: Regular updates and transparency about system goals
- Cultural Integration: Alignment with existing safety programs and values
Client Testimonial
"Visionify's AI-powered safety monitoring system has transformed how we approach workplace safety at our facility. The real-time insights and comprehensive coverage have allowed us to identify and address safety issues before they become incidents. Beyond the impressive reduction in compliance violations, we've seen a fundamental shift in our safety culture. Employees now take greater ownership of safety practices, knowing that consistent monitoring is in place. The system has become an invaluable partner in our commitment to ensuring everyone goes home safely every day."
— Mr. Ravikant A., EHS Lead.
Technology Overview
Our solution for the client leverages several advanced technologies to provide comprehensive safety monitoring:
Computer Vision AI
- Custom-trained models for chemical manufacturing environments
- Multi-class detection for various PPE types and safety violations
- Adaptive algorithms that function in challenging industrial conditions
- Continuous learning capabilities to improve over time
Edge Computing Architecture
- On-premise processing for sensitive operational data
- Low-latency analysis for real-time safety interventions
- Distributed processing across strategic facility locations
- Redundant systems to ensure continuous monitoring
Intelligent Analytics
- Pattern recognition to identify recurring safety issues
- Predictive capabilities to anticipate potential hazards
- Comprehensive reporting for regulatory compliance
- Actionable insights for safety program improvement
Visionify – Empowering Chemical Manufacturing Safety Through Vision AI
Our comprehensive safety monitoring solution provided the client with powerful tools to transform workplace safety at their facility. Through automated detection, intelligent alerts, and comprehensive analytics, Visionify not only helped reduce compliance violations but also enhanced operational efficiency and safety culture.
The client can now confidently operate their chemical manufacturing processes knowing that safety is being continuously monitored and improved. This successful partnership exemplifies how Visionify's innovative computer vision solutions can transform industrial safety through advanced AI technology.
Conclusion
This case study demonstrates how AI-powered vision technology can transform safety management in chemical manufacturing environments. By providing continuous monitoring, immediate feedback, and actionable insights, our safety monitoring solution enabled the client's facility to create a significantly safer workplace while improving operational efficiency.
The success of this implementation has led to discussions about expanding the system to additional facilities globally, with the northern India implementation serving as a model for best practices in AI-enhanced safety management.
Are you facing similar safety challenges in your manufacturing operations? Contact Visionify today to learn how our AI-powered safety monitoring solutions can transform your approach to workplace safety and compliance.
Frequently Asked Questions
Find answers to common questions about this implementation
Ready to achieve similar results?
Let us show you how our Vision AI safety solutions can transform your workplace safety.
Schedule a ConsultationRelated Case Studies
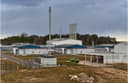
Case Study: How a Multi-Site Industrial Enterprise Leveraged Safety Insights with Visionify's Safety AI Platform
Manufacturing
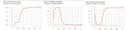
Case Study: How a Leading Irrigation Equipment Manufacturer Enhanced Drilling Precision with Visionify's AI Quality Check Solution
Manufacturing
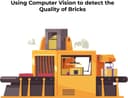
Case Study: Using Computer Vision to Detect the Quality of Bricks
Manufacturing
Schedule a Meeting
Book a personalized demo with our product specialists to see how our AI safety solutions can work for your business.
Choose a convenient time
Select from available slots in your timezone
30-minute consultation
Brief but comprehensive overview of our solutions
Meet our product experts
Get answers to your specific questions