Why Inline Barcode Verification Solution is better than Offline Solution?
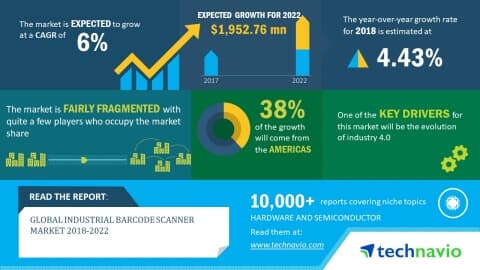
Key Takeaways
- Complete Inspection: Inline systems verify every barcode, not just random samples
- Real-Time Detection: Problems are identified immediately, preventing defective products from shipping
- Advanced Capabilities: Modern inline systems can verify 1D, 2D, and 3D codes at production speeds
- Comprehensive Reporting: Detailed quality metrics for every barcode produced
- Proactive Alerts: Early warning when barcode quality begins to deteriorate
Understanding Barcode Verification
Barcode verification is a critical quality control process that ensures barcodes meet industry standards for readability and accuracy. Unlike simple barcode reading, verification evaluates multiple parameters defined by ISO standards, including:
- Symbol contrast
- Minimum reflectance
- Modulation
- Decodability
- Defects
- Fixed pattern damage
- Quiet zone
Inline verification systems inspect every barcode at production speeds
Manufacturers implement barcode verification to ensure that their codes will be readable throughout the supply chain, regardless of the scanning equipment used. This verification process produces standardized quality grades (typically A through F) that objectively measure barcode performance.
The Traditional Approach: Offline Verification
Offline barcode verification has been the standard approach for decades, typically using desktop or handheld verification devices separate from the production line.
How Offline Verification Works:
- Sampling: Operators select random samples from production batches
- Manual Scanning: Each sample is individually scanned by the verification device
- Analysis: The device evaluates the barcode against ISO standards
- Reporting: Quality reports are generated for the sampled codes
- Batch Approval: The entire batch is approved or rejected based on sample results
Limitations of Offline Verification:
- Incomplete Coverage: Only a small percentage of barcodes are actually verified
- Delayed Detection: Quality issues may not be discovered until after production is complete
- Limited Diagnostics: When problems occur with non-sampled codes, no verification data exists
- Manual Process: Requires dedicated operator time for testing
- Production Interruption: May require stopping production to conduct verification
While offline verification systems are typically less expensive initially and require minimal setup, they provide only a statistical approximation of overall barcode quality rather than comprehensive verification.
The Advanced Approach: Inline Verification
Inline barcode verification integrates directly into the production line, examining every barcode as it's produced without slowing the manufacturing process.
How Inline Verification Works:
- Continuous Monitoring: Cameras mounted on the production line capture images of every barcode
- Real-Time Analysis: Computer vision algorithms immediately evaluate each code against ISO standards
- Instant Feedback: Quality issues are flagged in real-time
- Comprehensive Data: Verification metrics are recorded for every single barcode
- Trend Analysis: The system monitors quality trends to detect gradual degradation
Advantages of Inline Verification:
- 100% Inspection: Every barcode is verified, not just random samples
- Immediate Detection: Quality issues are identified as they occur
- Complete Traceability: Verification data exists for every code produced
- No Production Delays: Verification occurs at full production speed
- Preventive Maintenance: Early warning when print quality begins to deteriorate
- Reduced Waste: Problems are corrected before producing large quantities of defective codes
Recent Technological Advancements
Historically, inline verification systems were limited by processing speed and could only handle simple linear (1D) barcodes at modest production rates. However, recent technological advances have dramatically expanded their capabilities:
Speed Improvements:
Modern computer vision systems can now process images at rates compatible with high-speed production lines, eliminating the previous bottleneck.
Code Type Expansion:
Advanced inline systems can now verify:
- Traditional 1D barcodes (UPC, Code 128, etc.)
- 2D codes (QR codes, Data Matrix, etc.)
- Direct part marking (DPM)
- 3D codes with depth information
Lighting Innovations:
Sophisticated lighting systems can now:
- Provide consistent illumination at various angles
- Adjust automatically for different code types
- Meet ISO standards for verification lighting
- Accommodate various substrate materials
Integration Capabilities:
Modern systems offer:
- Direct connection to production equipment
- Integration with manufacturing execution systems (MES)
- Automated rejection mechanisms for failed codes
- Remote monitoring and reporting capabilities
Implementation Considerations
When evaluating inline barcode verification systems, manufacturers should consider several key factors:
1. Production Line Compatibility
- Space Requirements: Physical space needed for camera and lighting installation
- Line Speed: Maximum production rate the system can accommodate
- Environmental Factors: Dust, vibration, and lighting conditions
2. Code Specifications
- Code Types: The specific barcode symbologies being used
- Code Sizes: Minimum and maximum dimensions of barcodes
- Marking Methods: Printing technology or direct marking approach
3. Compliance Requirements
- Industry Standards: Specific ISO/IEC standards applicable to your industry
- Customer Requirements: Verification grades required by major customers
- Regulatory Considerations: Requirements for regulated industries like pharmaceuticals
4. System Integration
- Data Management: How verification data will be stored and analyzed
- Alert Mechanisms: How operators will be notified of quality issues
- Rejection Systems: Whether automatic rejection of failed codes is needed
Return on Investment
While inline verification systems typically require a higher initial investment than offline alternatives, they often deliver superior ROI through:
- Reduced Rework: Catching problems immediately rather than after batch completion
- Fewer Returns: Eliminating customer complaints due to unreadable barcodes
- Labor Savings: Eliminating manual sampling and verification processes
- Scrap Reduction: Minimizing waste from defective codes
- Compliance Assurance: Avoiding penalties or chargebacks for non-compliant codes
Conclusion
As manufacturing speeds increase and barcode applications become more critical, the limitations of traditional offline verification become increasingly problematic. Inline barcode verification systems offer a comprehensive solution by examining every code produced, providing immediate feedback, and enabling proactive quality management.
While the initial investment may be higher, the benefits of 100% inspection, real-time detection, and comprehensive data collection make inline verification the superior choice for manufacturers committed to quality and efficiency. By preventing defective barcodes from reaching customers, these systems protect brand reputation, reduce costs, and ensure smooth operation throughout the supply chain.
For manufacturers experiencing barcode reading issues or seeking to upgrade their quality control processes, image-based inline verification solutions offer a powerful tool for ensuring consistent, reliable barcode performance.
This article provides a historical perspective on barcode verification solutions. While Visionify now specializes in computer vision solutions for various industries, we recognize the continuing importance of automated inspection technologies in manufacturing environments.
Want to learn more?
Discover how our Vision AI safety solutions can transform your workplace safety.
Schedule a DemoSchedule a Meeting
Book a personalized demo with our product specialists to see how our AI safety solutions can work for your business.
Choose a convenient time
Select from available slots in your timezone
30-minute consultation
Brief but comprehensive overview of our solutions
Meet our product experts
Get answers to your specific questions
Related Articles
Subscribe to our newsletter
Get the latest safety insights and updates delivered to your inbox.