How to Select Machine Vision Cameras?
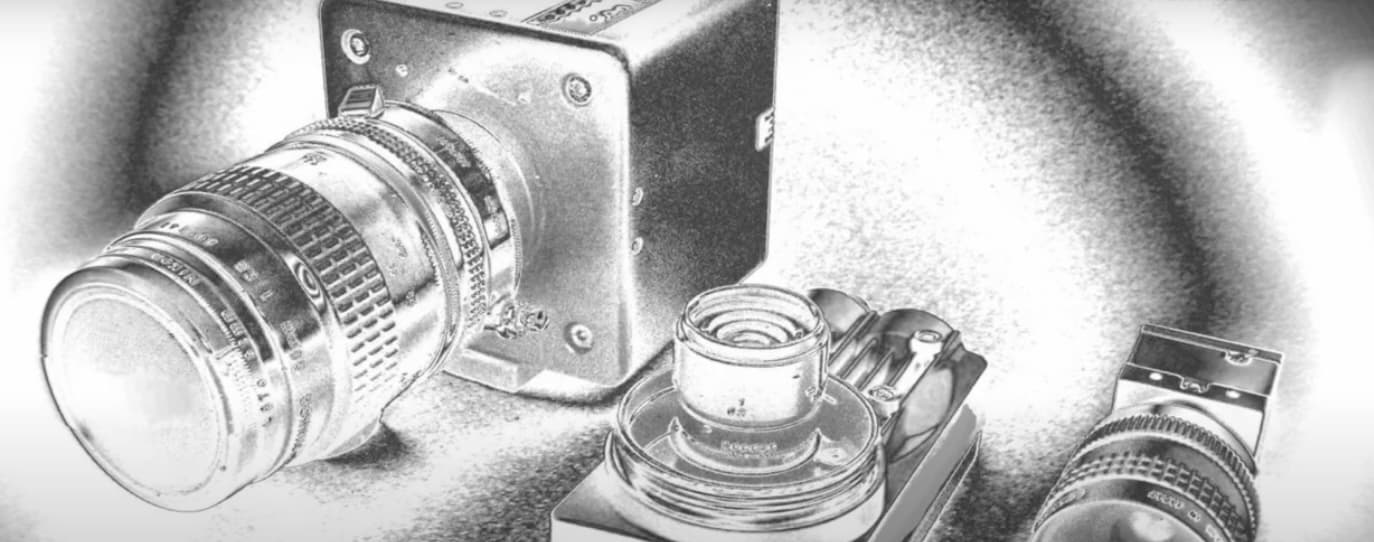
Key Takeaways
- Market Growth: The global machine vision market is expected to grow from $12.09 billion in 2021 to $13.52 billion in 2022
- Application-Driven: Camera selection should be based on specific application requirements
- Critical Specifications: Resolution, frame rate, sensor type, and interface are key selection factors
- Environmental Considerations: Operating conditions significantly impact camera performance
- System Integration: Camera selection must account for compatibility with other vision system components
The Expanding Role of Machine Vision
Machine vision technology continues to transform industrial processes across sectors. According to Report Linker, the global machine vision market is expected to grow from $12.09 billion in 2021 to $13.52 billion in 2022, driven by increasing demand for automated inspection and quality control systems.
As manufacturing becomes increasingly automated, machine vision cameras serve as the critical "eyes" of production systems, enabling precise inspection, measurement, and guidance that human vision cannot match in consistency, speed, or accuracy.
Understanding Machine Vision Camera Capabilities
Machine vision cameras perform a wide range of industrial functions:
- Quality Inspection: Detecting defects, inconsistencies, and anomalies
- Measurement: Precisely gauging dimensions and tolerances
- Identification: Reading barcodes, QR codes, and text
- Guidance: Directing robots and automated systems
- Verification: Ensuring correct assembly and packaging
- Sorting: Classifying products based on visual characteristics
These capabilities enable manufacturers to improve quality, increase throughput, reduce waste, and enhance safety across production environments.
Essential Selection Criteria
Choosing the right machine vision camera requires careful consideration of several key factors:
1. Resolution Requirements
Resolution determines the camera's ability to capture fine details:
- Standard Resolution (1-2MP): Suitable for basic inspection and presence verification
- Medium Resolution (3-5MP): Appropriate for detailed inspection and measurement
- High Resolution (8MP+): Necessary for precision applications and small feature detection
The required resolution depends on the size of the smallest feature that must be detected and the field of view needed for the application.
2. Sensor Technology
The image sensor is the heart of any vision camera:
- CCD (Charge-Coupled Device): Offers excellent image quality and low noise, but typically slower and more expensive
- CMOS (Complementary Metal-Oxide-Semiconductor): Provides faster frame rates, lower power consumption, and cost advantages
- Global vs. Rolling Shutter: Global shutter captures the entire image simultaneously, essential for moving objects; rolling shutter captures line by line, which can cause distortion with motion
For most modern applications, CMOS sensors with global shutter capability offer the best balance of performance and value.
3. Frame Rate
Frame rate determines how many images the camera can capture per second:
- Low Frame Rate (15-30 fps): Adequate for stationary inspection
- Medium Frame Rate (60-120 fps): Suitable for moderate-speed production lines
- High Frame Rate (200+ fps): Required for high-speed processes and motion analysis
Applications with moving objects or high-throughput production lines require higher frame rates to avoid motion blur and ensure accurate inspection.
4. Spectral Sensitivity
Different applications require sensitivity to different light wavelengths:
- Visible Spectrum: Standard for color-critical applications
- Infrared (IR): Useful for heat detection and seeing through certain materials
- Ultraviolet (UV): Valuable for detecting surface flaws and certain materials
- Multispectral: Combines multiple wavelength bands for enhanced detection capabilities
Matching the camera's spectral sensitivity to the application requirements is essential for optimal performance.
5. Interface and Connectivity
The camera interface affects data transfer speed, cable length, and system integration:
- GigE Vision: Offers long cable lengths (up to 100m) and network integration
- USB3 Vision: Provides high bandwidth with simple connectivity
- Camera Link: Delivers high data rates for demanding applications
- CoaXPress: Enables very high-speed data transfer over coaxial cables
- GenICam Compliance: Ensures compatibility with vision software platforms
The chosen interface must support the required data throughput while meeting installation constraints.
6. Environmental Considerations
Industrial environments often present challenging conditions:
- Temperature Range: Cameras must operate reliably in ambient conditions
- Ingress Protection (IP Rating): Determines resistance to dust and moisture
- Vibration Resistance: Critical for applications on moving machinery
- Lighting Conditions: Affects image quality and may require specialized illumination
- Space Constraints: May limit camera size and mounting options
Ruggedized cameras with appropriate IP ratings are essential for harsh industrial environments.
7. Software Compatibility
The camera must integrate with your machine vision software:
- SDK Availability: Software development kits for custom applications
- Driver Support: Compatibility with major vision software platforms
- Processing Capabilities: On-board processing vs. external computing requirements
- Feature Sets: Support for required functions like triggering and image pre-processing
Ensuring software compatibility prevents integration challenges during implementation.
Implementation Best Practices
When implementing machine vision cameras, consider these best practices:
- Test Before Committing: Evaluate camera performance with actual parts and conditions
- Consider Future Needs: Select cameras that can accommodate potential application changes
- Standardize When Possible: Using consistent camera models simplifies maintenance and spares
- Plan for Proper Lighting: Even the best camera performs poorly with inadequate illumination
- Consult Experts: Work with vision system integrators for complex applications
Conclusion
Selecting the right machine vision camera is a critical decision that impacts the performance, reliability, and cost-effectiveness of your vision system. By carefully evaluating resolution requirements, sensor technology, frame rate, spectral sensitivity, interface options, environmental factors, and software compatibility, you can choose a camera that meets your current needs while providing flexibility for future applications.
As machine vision technology continues to advance, cameras are becoming more powerful, compact, and affordable, opening new possibilities for automation and quality control across industries. Investing time in proper camera selection pays dividends through improved inspection accuracy, increased throughput, and enhanced manufacturing quality.
This article provides a historical perspective on machine vision camera selection. While Visionify now specializes in computer vision solutions for various industries, we recognize the continuing importance of hardware selection in building effective vision systems.
Want to learn more?
Discover how our Vision AI safety solutions can transform your workplace safety.
Schedule a DemoSchedule a Meeting
Book a personalized demo with our product specialists to see how our AI safety solutions can work for your business.
Choose a convenient time
Select from available slots in your timezone
30-minute consultation
Brief but comprehensive overview of our solutions
Meet our product experts
Get answers to your specific questions
Table of Contents
Related Articles
Subscribe to our newsletter
Get the latest safety insights and updates delivered to your inbox.