How Machine Vision is Revolutionizing Food Industry?
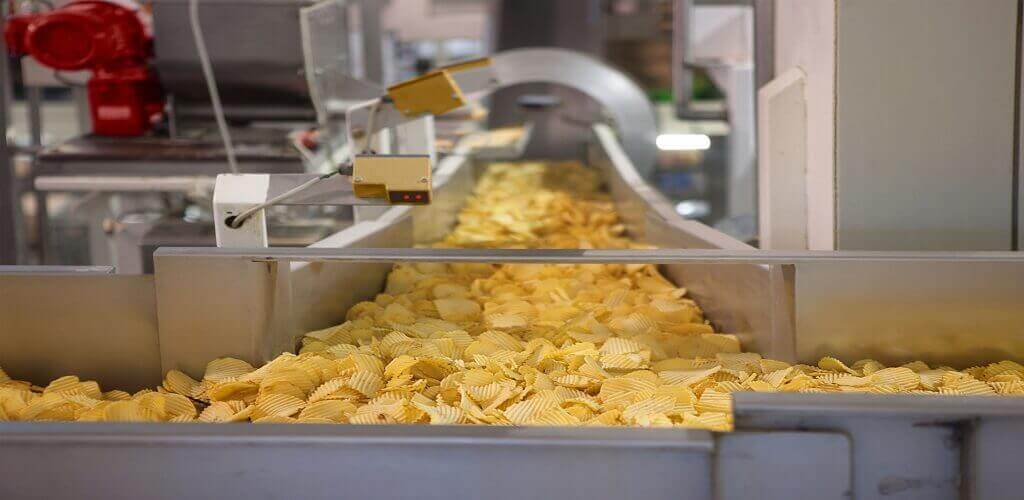
Key Takeaways
- Market Growth: Machine vision software in food processing is projected to reach $18.47 billion by 2028
- Quality Assurance: Automated visual inspection ensures consistent product quality and safety
- Efficiency Gains: Vision systems increase throughput while maintaining inspection standards
- Traceability: Advanced tracking capabilities enhance food safety and regulatory compliance
- Reduced Waste: Precise detection of defects minimizes product rejection and material waste
The Growing Importance of Vision Technology in Food Processing
The food industry faces unprecedented challenges in maintaining quality, safety, and efficiency while meeting growing consumer demands. Machine vision technology has emerged as a critical solution to these challenges, with market projections reflecting its increasing adoption. According to Absolute Reports, machine vision software in the food sector is predicted to grow from $9.07 billion in 2021 to $18.47 billion by 2028.
Advanced vision systems can detect subtle quality issues in food products at high production speeds
This remarkable growth reflects the transformative impact vision systems are having across all aspects of food production, from initial ingredient inspection to final packaging verification. While machine vision has been used in manufacturing for over 50 years, recent advances in computing power, sensor technology, and artificial intelligence have dramatically expanded its capabilities and applications in food processing.
Three Key Applications Transforming Food Production
Machine vision is revolutionizing the food industry through three primary applications:
1. Tracking and Traceability
Food traceability has become essential for regulatory compliance, consumer confidence, and efficient recall management. Machine vision systems provide unprecedented tracking capabilities:
- Ingredient Tracking: Following raw materials from reception through processing
- Batch Identification: Automatically reading and verifying batch codes and production dates
- Supply Chain Visibility: Maintaining complete documentation of product movement
- Recall Precision: Quickly identifying affected products in case of contamination
These capabilities not only enhance food safety but also improve inventory management and production planning. By automating the tracking process, manufacturers gain real-time visibility into their operations while reducing the administrative burden of manual record-keeping.
2. Safety and Quality Inspection
Perhaps the most critical application of machine vision in food processing is automated inspection:
- Foreign Object Detection: Identifying contaminants like plastic, metal, or glass
- Defect Recognition: Spotting discoloration, malformation, or texture abnormalities
- Size and Shape Verification: Ensuring dimensional consistency
- Color Analysis: Verifying proper cooking, ripeness, or freshness
- Surface Inspection: Detecting cracks, breaks, or other surface defects
Modern vision systems can inspect hundreds of items per minute with consistent accuracy, far exceeding human capabilities. These systems operate continuously without fatigue, maintaining vigilant quality control throughout production shifts.
The technology is particularly valuable for detecting subtle defects that might be missed by human inspectors, such as small discolorations or minor shape irregularities. By identifying these issues early in the production process, manufacturers can address problems before they result in wasted product or customer complaints.
3. Packaging Verification
Packaging errors represent a significant source of product recalls and consumer complaints. Machine vision systems ensure packaging integrity and accuracy:
- Seal Inspection: Verifying proper sealing of packages to maintain freshness
- Label Verification: Ensuring correct and properly applied labels
- Date Code Validation: Confirming readable and accurate expiration dates
- Fill Level Checking: Measuring proper product quantity in containers
- Package Integrity: Detecting damaged or defective packaging
These automated inspections prevent costly errors such as mislabeled allergens or incorrect nutritional information, which could lead to serious health risks and expensive recalls.
Implementation Considerations
Food manufacturers implementing machine vision should consider several factors:
- Environmental Challenges: Food processing environments often involve moisture, temperature variations, and sanitation requirements that affect system design
- Product Variability: Natural food products have inherent variations that must be accommodated in detection algorithms
- Line Speed Requirements: Vision systems must operate at production speeds without creating bottlenecks
- Integration Needs: Systems should connect with existing production equipment and data management platforms
- Regulatory Compliance: Solutions must meet food safety standards and documentation requirements
Successful implementations typically involve close collaboration between vision system providers, production engineers, and quality assurance teams to ensure the technology addresses specific operational needs.
Future Trends in Food Industry Machine Vision
Several emerging trends are shaping the future of machine vision in food processing:
- Hyperspectral Imaging: Detecting properties invisible to the human eye, such as internal defects or chemical composition
- AI and Deep Learning: Improving detection accuracy for complex or variable products
- Miniaturization: Smaller, more affordable systems making the technology accessible to smaller producers
- Cloud Integration: Connecting vision systems to cloud platforms for data analysis and remote monitoring
- Collaborative Robotics: Combining vision systems with robots for automated sorting and handling
These advances will further enhance the capabilities of machine vision systems while making them more accessible and cost-effective for food manufacturers of all sizes.
Conclusion
Machine vision technology has evolved from a specialized tool to an essential component of modern food processing operations. By automating inspection tasks, ensuring traceability, and verifying packaging integrity, these systems help manufacturers maintain product quality and safety while improving operational efficiency.
As consumer expectations for food quality and safety continue to rise, and regulatory requirements become increasingly stringent, machine vision will play an increasingly vital role in helping food manufacturers meet these challenges. For companies seeking to remain competitive in this demanding industry, implementing machine vision is no longer optional—it's becoming a necessity for maintaining quality, efficiency, and market position.
This article provides a historical perspective on machine vision in the food industry. While Visionify now specializes in computer vision solutions for various industries, we recognize the continuing importance of visual inspection technologies in ensuring food safety and quality.
Want to learn more?
Discover how our Vision AI safety solutions can transform your workplace safety.
Schedule a DemoSchedule a Meeting
Book a personalized demo with our product specialists to see how our AI safety solutions can work for your business.
Choose a convenient time
Select from available slots in your timezone
30-minute consultation
Brief but comprehensive overview of our solutions
Meet our product experts
Get answers to your specific questions
Related Articles
Subscribe to our newsletter
Get the latest safety insights and updates delivered to your inbox.