Finding Labeling Errors is Now Easy with Automated Visual Inspection
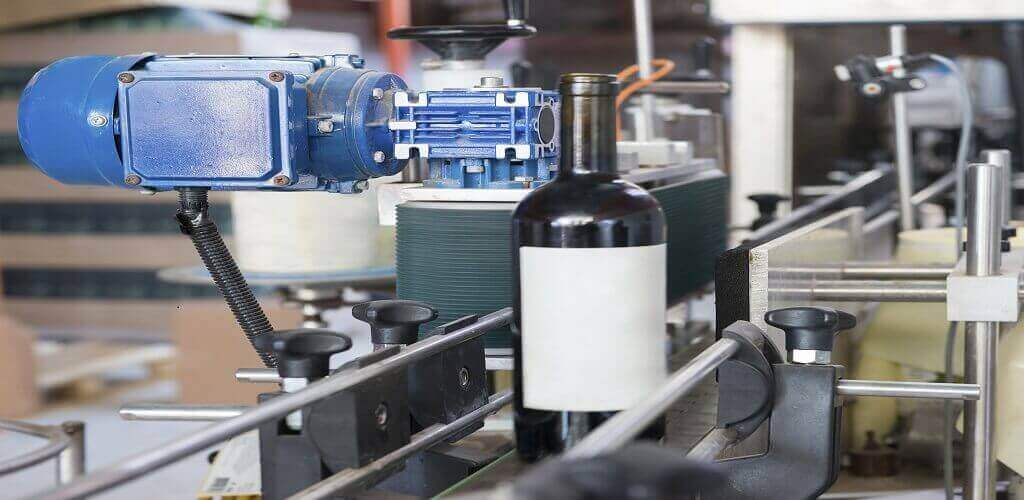
Key Takeaways
- Market Growth: The global label applicator market is projected to grow from $2.6 billion in 2022 to $3.5 billion by 2028
- Human Limitations: Manual inspectors can only process 10-12 images per second while production lines move much faster
- Comprehensive Detection: AI systems can simultaneously check label position, content, print quality, and barcode validity
- Critical Safety: Proper labeling is essential for consumer safety, particularly regarding allergen information
- ROI Benefits: Automated inspection reduces recall risks, labor costs, and regulatory penalties
The Labeling Challenge
When you encounter a product without a label or with incorrect information, you're witnessing a failure in quality control that has significant implications. For manufacturers, labeling errors represent more than just an aesthetic issue—they can lead to regulatory penalties, costly recalls, and even consumer safety risks.
Despite technological advancements in labeling systems, errors remain prevalent across manufacturing industries. From missing allergen warnings to misaligned labels and incorrect barcodes, these mistakes can have serious consequences for both consumers and companies.
The global market for label applicators is experiencing significant growth
The Limitations of Manual Inspection
Traditional quality control for labeling relies heavily on human visual inspection, which presents several challenges:
Speed Constraints
Human inspectors can process only 10-12 images per second, while modern production lines move at speeds of 12 inches or more per second. This fundamental mismatch makes comprehensive inspection impossible for human operators.
Fatigue Factors
Visual inspection is mentally taxing, and human attention inevitably wanes over time. Studies show that inspection accuracy can drop by up to 30% after just 30 minutes of continuous work.
Consistency Issues
Different inspectors may apply slightly different standards, leading to inconsistent quality control across shifts and production runs.
Scale Problems
For large manufacturers producing millions of units, the sheer volume makes manual inspection economically unfeasible.
The Automated Visual Inspection Solution
Computer vision technology, powered by artificial intelligence, offers a transformative approach to label inspection. These systems can process visual information at speeds far exceeding human capabilities while maintaining consistent accuracy.
System Components
A typical automated visual inspection system for labeling includes:
- High-Resolution Cameras: Capture detailed images of each product label
- Specialized Lighting: Ensures optimal visibility of label features
- Image Processing Hardware: Analyzes images in real-time
- AI Software: Makes pass/fail decisions based on learned parameters
- Rejection Mechanisms: Remove non-compliant products from the line
Inspection Process
The AI-powered inspection process follows several sophisticated steps:
Image Preprocessing
Before analysis, the system enhances image quality by:
- Adjusting contrast and brightness
- Removing noise and artifacts
- Enhancing edges and features
Image Segmentation
The system divides each image into recognizable sections for analysis:
- Label boundaries
- Text regions
- Barcode areas
- Logo elements
Feature Extraction
Key characteristics are identified and measured:
- Character recognition for text verification
- Geometric measurements for position checking
- Pattern matching for design verification
Classification and Decision
The system compares extracted features against reference standards to make quality decisions:
- Pass: Label meets all quality parameters
- Fail: Label contains errors requiring rejection
Key Inspection Capabilities
Automated visual inspection systems excel at detecting various labeling issues:
Position Verification
The system ensures labels are correctly placed by:
- Measuring distances from product edges
- Checking for proper alignment
- Verifying label is not wrinkled or bubbled
Text Verification
Using Optical Character Recognition (OCR), the system:
- Confirms product names and descriptions
- Verifies batch codes and expiration dates
- Checks ingredient lists for accuracy
- Cross-references allergen warnings with ingredients
Barcode Validation
The system ensures product traceability by:
- Verifying barcode presence
- Checking barcode readability
- Confirming barcode content matches product
Print Quality Assessment
The system examines the physical characteristics of the label:
- Checks for smudges or ink issues
- Identifies faded or incomplete printing
- Detects color variations outside acceptable ranges
Implementation Approach
Organizations implementing automated visual inspection should follow these steps:
1. Needs Assessment
- Identify current labeling error rates and types
- Determine which errors have the highest business impact
- Establish clear inspection criteria and tolerances
2. System Selection
- Choose hardware appropriate for production line speed
- Select software with learning capabilities for your specific products
- Ensure integration compatibility with existing systems
3. Training and Calibration
- Provide diverse examples of both acceptable and defective labels
- Calibrate detection sensitivity to balance false positives and negatives
- Test thoroughly across product variations
4. Integration and Workflow
- Position inspection systems at optimal points in the production line
- Establish clear protocols for handling rejected products
- Create feedback loops to address systematic issues
Business Benefits
Implementing automated visual inspection for labeling delivers multiple advantages:
Quality Assurance
- Consistent inspection criteria applied to every product
- Comprehensive documentation of inspection results
- Early detection of systematic labeling issues
Cost Reduction
- Fewer product recalls and returns
- Reduced waste from labeling errors
- Lower labor costs for quality control
Operational Efficiency
- Faster production speeds without sacrificing quality
- Reduced line stoppages for manual inspection
- Data-driven insights for process improvement
Regulatory Compliance
- Consistent adherence to labeling regulations
- Detailed inspection records for audit purposes
- Reduced risk of non-compliance penalties
Future Developments
As AI and computer vision technology continue to evolve, we can expect:
- Enhanced Learning Capabilities: Systems that improve accuracy through continuous operation
- Expanded Detection Parameters: More sophisticated analysis of label characteristics
- Integration with Other Systems: Coordination with inventory and production planning
- Predictive Maintenance: Early identification of labeling equipment issues
Conclusion
Automated visual inspection represents a significant advancement in manufacturing quality control for product labeling. By overcoming the limitations of manual inspection, these AI-powered systems help manufacturers ensure consistent labeling quality at production speeds.
For companies concerned about labeling errors, regulatory compliance, and consumer safety, automated visual inspection offers a compelling solution that delivers both immediate quality improvements and long-term cost savings. As the technology continues to advance, it will become an increasingly essential component of modern manufacturing operations.
This article provides a historical perspective on automated visual inspection for labeling. While Visionify now specializes in computer vision solutions for various industries, we recognize the continuing importance of vision-based systems in manufacturing quality control.
Frequently Asked Questions
Find answers to common questions about this topic
Want to learn more?
Discover how our Vision AI safety solutions can transform your workplace safety.
Schedule a DemoSchedule a Meeting
Book a personalized demo with our product specialists to see how our AI safety solutions can work for your business.
Choose a convenient time
Select from available slots in your timezone
30-minute consultation
Brief but comprehensive overview of our solutions
Meet our product experts
Get answers to your specific questions
Subscribe to our newsletter
Get the latest safety insights and updates delivered to your inbox.