Case Study: AI-Powered Leakage Detection in the Beverage Industry
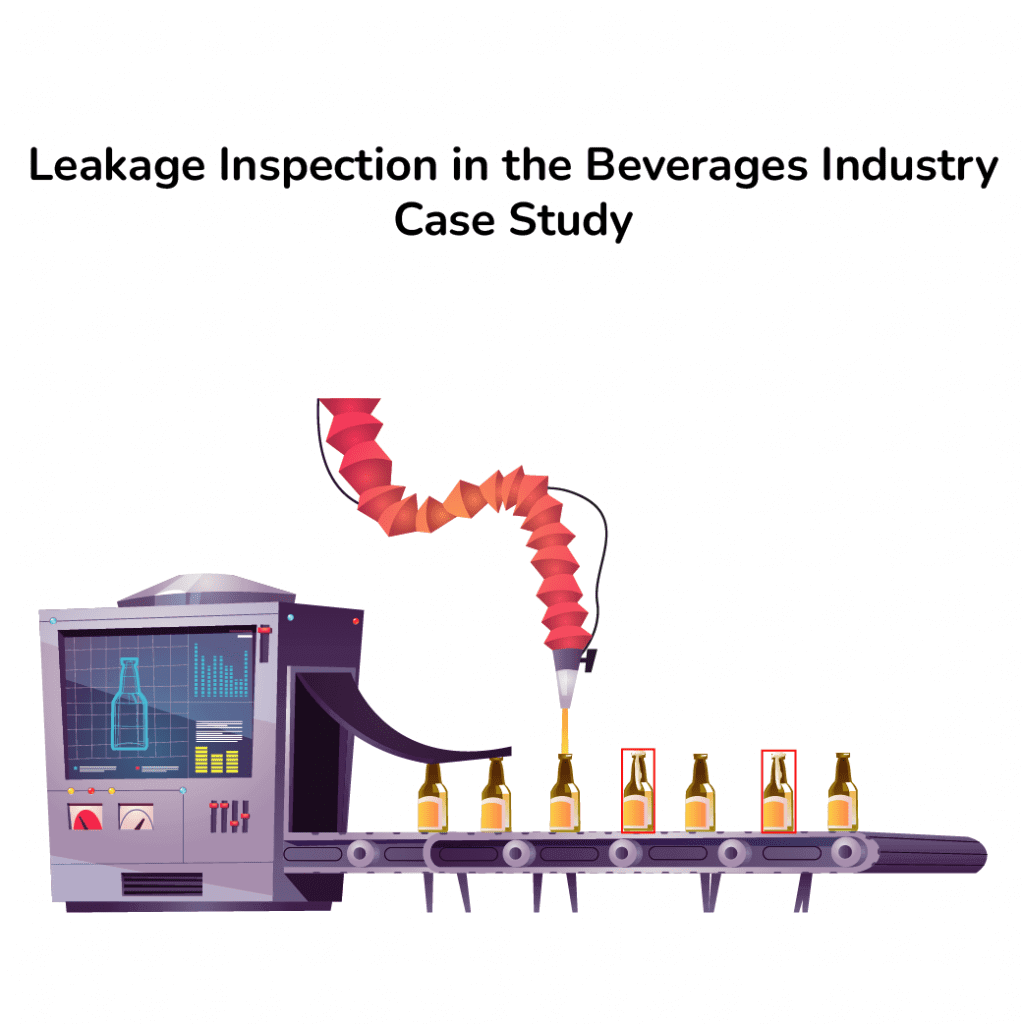
Client Profile
Industry: Beverage Manufacturing
Size: Large brewery with multiple production facilities
Location: North America
Production Volume: 2.5 million kegs annually
Our client is one of the largest craft breweries in North America, producing a wide range of beer products distributed nationally and internationally. With a strong commitment to quality and sustainability, they were seeking ways to minimize product loss and improve efficiency in their keg filling operations.
The Challenge
Despite significant investments in production technology, the client was experiencing persistent challenges with their keg inspection process:
- Product Loss: Approximately 1.2% of filled kegs experienced leakage, resulting in significant product waste and revenue loss.
- Manual Inspection Limitations: Human inspectors could only examine a small percentage of kegs, missing many defects.
- Inconsistent Detection: Manual inspection was subjective and varied between inspectors and shifts.
- Production Bottlenecks: The inspection process created slowdowns in the production line.
- Environmental Concerns: Product leakage created cleaning challenges and environmental issues.
- Quality Reputation: Occasional leaking kegs reached customers, damaging the brand's quality reputation.
The Production Director explained their situation: "Keg leakage was costing us hundreds of thousands of dollars annually in lost product, not to mention the environmental impact and potential damage to our brand reputation. Our manual inspection process simply couldn't keep pace with our production volume or provide the level of accuracy we needed."
The Solution
After evaluating several options, the brewery partnered with Visionify to implement an AI-powered Computer Vision Leakage Detection System for their keg filling lines:
1. Automated Inspection System
- Installation of high-speed industrial cameras in light-controlled tunnels
- Custom lighting setup optimized for detecting foam and liquid leakage
- Integration with existing conveyor systems
- Real-time image capture and analysis of each keg after filling
2. Advanced Leakage Detection
- Computer vision algorithms specifically trained to identify:
- Foam structures indicating leaks
- Liquid seepage around fittings
- Dents and scratches that might compromise keg integrity
- Fitting surface damage
- Machine learning models capable of distinguishing between condensation and actual leakage
3. Intelligent Classification System
- Multi-parameter image capture to analyze foam-to-structure ratios
- Customizable rejection thresholds based on severity of detected issues
- Automated sorting of defective kegs for repair or refilling
- Detailed documentation of each detected defect with images
4. Ultrasonic Verification System
- Secondary verification using ultrasonic bath technology
- Conveyor system passing through water-filled tub with ultrasonic activators
- Enhanced detection of microscopic leaks not visible to cameras
- Complementary approach combining visual and ultrasonic detection
5. Quality Analytics Platform
- Comprehensive reporting on defect types, frequencies, and trends
- Production line performance metrics
- Batch-specific quality statistics
- Early warning system for emerging quality issues
Implementation Process
The implementation followed a structured approach to ensure minimal disruption to production:
-
Assessment & Planning (3 weeks)
- Comprehensive analysis of current keg filling and inspection processes
- Identification of optimal inspection points in the production line
- Camera and lighting placement planning
- Development of integration strategy with existing systems
-
Pilot Deployment (4 weeks)
- Installation on one keg filling line
- Initial model training with thousands of keg images
- Calibration of detection thresholds and classification parameters
- Side-by-side comparison with manual inspection results
-
Model Refinement (3 weeks)
- Analysis of false positives and false negatives
- Additional training to improve detection accuracy
- Fine-tuning of classification thresholds to optimize rejection rates
- Validation against expert human inspectors
-
Full-Scale Implementation (8 weeks)
- Phased rollout across all keg filling lines
- Integration with production management systems
- Comprehensive training for quality control and production staff
- Development of standard operating procedures
-
Continuous Improvement (Ongoing)
- Regular model updates based on new keg types and beer products
- Periodic retraining with new production data
- System optimization for different environmental conditions
- Addition of new detection capabilities as needed
Results
After six months of operation, the Leakage Detection System delivered significant improvements across multiple performance metrics:
Quality Improvements
- 96% reduction in undetected keg leakage
- Rejection rate maintained at 0.2% of total production
- Error rate reduced to 0.05% (false positives/negatives)
- Inspection capacity of 1,400 kegs per hour
- 3-second inspection cycle per keg
Operational Efficiencies
- 28% increase in production throughput
- 65% reduction in quality control labor costs
- 24/7 operation without inspection fatigue or variability
- Real-time quality feedback to production teams
- Automated documentation of fitting accuracy
Financial Impact
- Annual savings of $420,000 in reduced product loss
- $180,000 decrease in labor costs
- Increased revenue from higher production throughput
- ROI of 310% within the first year
- Payback period of 3.9 months
Additional Benefits
- Environmental Impact: Significant reduction in beer waste and associated water usage for cleanup
- Enhanced Brand Reputation: Elimination of leaking kegs reaching customers
- Data-Driven Insights: Identification of patterns in defects led to upstream process improvements
- Better Resource Allocation: Quality control staff focused on process improvement rather than routine inspection
- Improved Sustainability Metrics: Reduced waste contributed to company's environmental goals
Key Success Factors
Several elements were crucial to the project's success:
-
Specialized Imaging Techniques: Custom approach to capturing and analyzing foam structures.
-
Environmental Controls: Light-protective tunnels to ensure consistent image quality.
-
Multi-Parameter Analysis: Capturing successive images with varying parameters to accurately distinguish leaks from condensation.
-
Dual-Technology Approach: Combining computer vision with ultrasonic verification for comprehensive detection.
-
Production Integration: Seamless incorporation into existing filling lines without major modifications.
Implementation Challenges & Solutions
The project faced several challenges during implementation:
-
Moist Environment
- Challenge: High humidity and condensation in the filling area complicated leak detection
- Solution: Development of specialized algorithms to distinguish between condensation and actual leakage
-
Foam Variability
- Challenge: Different beer products produced varying foam patterns
- Solution: Training the system with product-specific datasets and implementing adaptive detection parameters
-
Production Speed
- Challenge: High-speed production lines required rapid inspection decisions
- Solution: Optimization of image processing algorithms and implementation of parallel computing architecture
-
Keg Variability
- Challenge: Multiple keg types and sizes in production
- Solution: Development of flexible detection models that could adapt to different keg configurations
Client Testimonial
"Visionify's leakage detection system has transformed our keg filling operation. We're now able to inspect every single keg with a level of accuracy that was impossible before. The reduction in product loss alone justified the investment, but we've also seen significant improvements in production efficiency and sustainability metrics. The system's ability to distinguish between actual leaks and condensation has been particularly impressive, virtually eliminating false rejections while catching real issues."
— James K., Director of Brewing Operations
Technology Overview
Our solution leverages several advanced technologies to provide accurate, high-speed keg inspection:
Specialized Imaging System
- High-resolution industrial cameras capture detailed images of each keg
- Controlled lighting environment to highlight foam and liquid patterns
- Multiple imaging angles to ensure comprehensive coverage
- Sequential imaging with varying parameters to enhance detection accuracy
Advanced Detection Algorithms
- Custom computer vision algorithms trained specifically for beer foam patterns
- Deep learning models that can distinguish between condensation and leakage
- Pattern recognition for identifying fitting damage and keg deformities
- Real-time image processing for immediate decision-making
Ultrasonic Verification
- Integration with ultrasonic testing for verification of critical cases
- Water-filled tub with ultrasonic activators to detect microscopic leaks
- Complementary approach combining visual and ultrasonic detection
- Enhanced accuracy through multi-modal inspection
Analytics and Documentation
- Comprehensive tracking of leakage statistics by batch
- Continuous documentation of fitting accuracy
- Trend analysis to identify recurring issues
- Predictive maintenance indicators based on defect patterns
Visionify – Empowering Beverage Quality Through Vision AI
Our Computer Vision Leakage Detection solution provided our client with powerful tools to overcome their keg inspection challenges. Through automated detection, intelligent classification, and comprehensive analytics, Visionify not only helped reduce product loss but also enhanced production efficiency and sustainability.
Our client can now confidently distribute their beer products knowing that virtually all leakage issues are detected before kegs leave the facility. This successful implementation exemplifies how Visionify's innovative computer vision solutions can transform beverage manufacturing quality control through advanced AI technology.
Conclusion
This case study demonstrates how computer vision technology can revolutionize leakage detection in the beverage industry. By implementing an AI-powered inspection system, our client was able to significantly reduce product loss while improving production efficiency and environmental performance.
The success of this implementation has led to the brewery exploring additional applications of computer vision technology in their manufacturing processes, including label inspection and fill-level verification. The data collected from the system has also provided valuable insights for process improvements that have further enhanced product quality and production efficiency.
Are you facing similar quality control challenges in your beverage manufacturing operations? Contact Visionify today to learn how our Computer Vision solutions can transform your approach to product quality and production efficiency.
Ready to achieve similar results?
Let us show you how our Vision AI safety solutions can transform your workplace safety.
Schedule a ConsultationRelated Case Studies
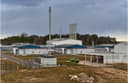
Case Study: How a Multi-Site Industrial Enterprise Leveraged Safety Insights with Visionify's Safety AI Platform
Manufacturing
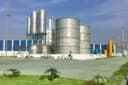
Case Study: How a Global Chemical Manufacturer Transformed Workplace Safety with Visionify's AI Solutions
Manufacturing
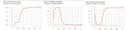
Case Study: How a Leading Irrigation Equipment Manufacturer Enhanced Drilling Precision with Visionify's AI Quality Check Solution
Manufacturing
Schedule a Meeting
Book a personalized demo with our product specialists to see how our AI safety solutions can work for your business.
Choose a convenient time
Select from available slots in your timezone
30-minute consultation
Brief but comprehensive overview of our solutions
Meet our product experts
Get answers to your specific questions