Best Ways to Prevent No Reads With Barcode Testing
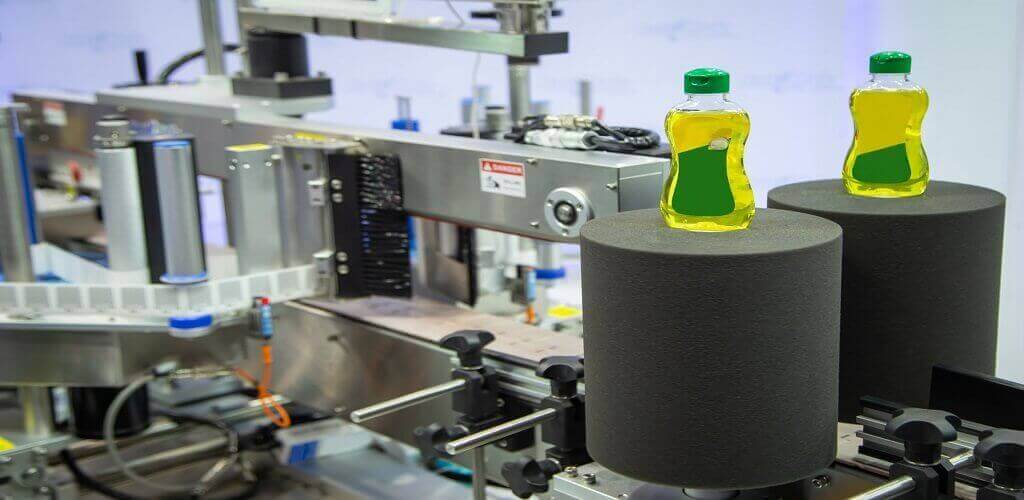
Key Takeaways
- Market Growth: The industrial barcode scanner market is projected to grow by $388.38 million at a 5% CAGR from 2021-2025
- Cost Impact: No-reads require manual intervention, wasting time and introducing potential errors
- Verification vs. Reading: Barcode verifiers diagnose specific problems, while readers only indicate success or failure
- Systematic Approach: Effective prevention requires proper equipment selection, testing protocols, and consistent monitoring
- Implementation Options: Companies can choose between continuous inline verification or strategic sampling approaches
Understanding the No-Read Problem
A "no-read" occurs when a barcode scanner fails to successfully decode a barcode. This seemingly minor issue can have significant consequences in manufacturing and logistics operations:
- Productivity Loss: Workers must manually enter data, slowing down operations
- Error Introduction: Manual entry increases the risk of data errors
- Traceability Gaps: Unreadable codes create holes in product tracking systems
- Customer Rejections: Trading partners may refuse shipments with poor quality barcodes
- Compliance Issues: Regulated industries face potential penalties for traceability failures
Modern barcode verification system analyzing code quality parameters
Why No-Reads Occur
Barcode reading failures stem from multiple potential causes:
Print Quality Issues
- Insufficient contrast between bars and spaces
- Inconsistent ink density or distribution
- Voids or spots in the code
- Bleeding or spreading of ink
Dimensional Problems
- Barcodes printed too small or too large
- Improper aspect ratios
- Insufficient quiet zones (margins)
- Bar width deviations
Environmental Factors
- Inadequate lighting
- Reflective packaging materials
- Curved or irregular surfaces
- Physical damage during handling
Three-Step Prevention Strategy
1. Choose the Right Verification Equipment
Selecting appropriate verification technology is the foundation of no-read prevention:
- Match to Symbology: Ensure verifiers support the specific barcode types you use
- Field of View Considerations: Verify the system can accommodate your smallest and largest codes
- Standards Compliance: Select equipment certified to relevant standards (ISO, GS1)
- Ease of Integration: Consider software compatibility with existing systems
2. Establish a Testing Protocol
Develop a systematic approach to barcode verification:
- Regular Testing Schedule: Define when and how often codes will be verified
- Grading Parameters: Establish minimum acceptable quality grades
- Failure Response Plan: Create clear procedures for addressing quality issues
- Documentation Requirements: Maintain records of verification results
- Root Cause Analysis: Implement processes to identify and address underlying problems
3. Implement Appropriate Sampling Methods
Choose between two primary verification approaches:
Random Sampling
- Test representative samples at predetermined intervals
- Suitable for stable processes with consistent quality
- Requires less capital investment
- May miss intermittent problems
Inline Verification
- Verifies 100% of barcodes during production
- Provides immediate feedback on quality issues
- Prevents bad codes from entering the supply chain
- Requires more sophisticated equipment and integration
Verification vs. Reading: Understanding the Difference
A critical distinction exists between barcode readers and verifiers:
Barcode Readers
- Provide binary feedback (read/no-read)
- Optimized for speed in operational environments
- Cannot diagnose specific quality issues
- May compensate for marginal quality, masking potential problems
Barcode Verifiers
- Measure multiple quality parameters
- Provide detailed diagnostics and grades
- Identify specific issues affecting readability
- Help predict performance across different scanning environments
Conclusion
Preventing barcode no-reads requires a proactive, systematic approach to quality control. By implementing proper verification equipment, establishing clear testing protocols, and choosing appropriate sampling methods, manufacturers can significantly reduce or eliminate no-reads.
The investment in barcode verification pays dividends through improved operational efficiency, reduced manual intervention, enhanced traceability, and stronger trading partner relationships. As the industrial barcode scanner market continues to grow, verification will play an increasingly important role in ensuring smooth, error-free operations.
For manufacturers seeking to eliminate barcode reading problems, Visionify offers multi-level label checking solutions that detect various label defects, ensuring products ship with zero label issues and maximizing customer satisfaction.
This article provides a historical perspective on barcode verification in manufacturing. While Visionify now specializes in computer vision solutions for various industries, we recognize the continuing importance of vision-based systems in quality control and traceability applications.
Frequently Asked Questions
Find answers to common questions about this topic
Want to learn more?
Discover how our Vision AI safety solutions can transform your workplace safety.
Schedule a DemoSchedule a Meeting
Book a personalized demo with our product specialists to see how our AI safety solutions can work for your business.
Choose a convenient time
Select from available slots in your timezone
30-minute consultation
Brief but comprehensive overview of our solutions
Meet our product experts
Get answers to your specific questions
Related Articles
Subscribe to our newsletter
Get the latest safety insights and updates delivered to your inbox.