What are the challenges of On-Shelf Availability and how they are solved?
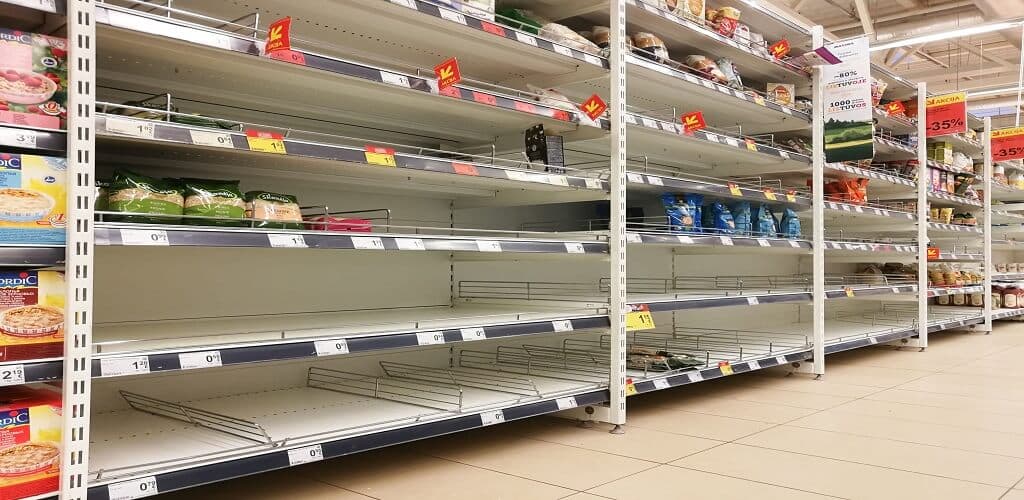
Key Takeaways
- Consumer Impact: When products are unavailable, 49% of shoppers buy substitutes, 39% leave without purchasing, and 12% visit competitors
- Revenue Loss: Manufacturers can lose up to 3.9% of sales due to poor on-shelf availability
- Root Causes: 60% of out-of-stock instances stem from in-store execution issues rather than supply chain problems
- Traditional Limitations: Current measurement methods like POS data and manual audits lack real-time accuracy
- Technology Solution: Computer vision and AI provide continuous, accurate shelf monitoring
Understanding On-Shelf Availability
On-Shelf Availability (OSA) refers to the presence of products in saleable condition on store shelves when and where customers expect to find them. Despite the growth of e-commerce, physical retail remains crucial to the shopping experience, with many consumers preferring to see products before purchasing. However, this experience is undermined when items are unavailable on shelves.
Computer vision systems can continuously monitor product availability on retail shelves
According to Global Market Insights, the AI in Retail market exceeded USD 2 billion in 2020 and is projected to grow at a rate of more than 30% between 2021 and 2027. This growth reflects the increasing adoption of technologies designed to address critical retail challenges, including on-shelf availability.
The Business Impact of Poor OSA
The consequences of poor on-shelf availability extend beyond immediate lost sales:
For Retailers:
- Lost Sales: Immediate revenue loss when customers cannot find products
- Reduced Customer Loyalty: Shoppers may switch to competitors after repeated disappointments
- Inefficient Operations: Staff time wasted on reactive replenishment
- Inaccurate Demand Signals: Out-of-stocks distort true demand patterns
For Manufacturers:
- Revenue Loss: Up to 3.9% of potential sales lost due to poor availability
- Brand Perception: Products perceived as unreliable when consistently unavailable
- Promotional Ineffectiveness: Marketing investments wasted when products aren't available
- Competitive Disadvantage: Competitors gain market share when products are missing
Key Challenges Affecting On-Shelf Availability
Several factors contribute to poor on-shelf availability in retail environments:
1. Planning and Management Gaps
Approximately 20% of out-of-stock cases stem from poor communication between manufacturers and retailers. This includes:
- Discontinued products remaining in planograms
- Insufficient allocation of shelf space
- Misalignment between shipped inventory and shelf capacity
- Poor planogram compliance
2. Forecasting Inaccuracies
Retailers must estimate demand and place orders in advance, but several factors can lead to forecasting errors:
- Unexpected demand spikes during promotions
- Seasonal fluctuations not properly accounted for
- New product introductions with limited historical data
- External factors like weather events or local activities
3. Store Ordering Issues
Even with accurate forecasts, ordering problems can create availability gaps:
- Late placement of replenishment orders
- Insufficient order quantities
- Minimum order quantity constraints
- Order frequency limitations
4. In-Store Execution Problems
Up to 60% of out-of-stock instances are caused by flaws in store-level execution rather than upstream supply chain issues:
- Products in backrooms not reaching shelves
- Incorrect shelf placement
- Inaccurate labeling or UPC codes
- Insufficient staff for timely replenishment
Limitations of Traditional Measurement Methods
Current approaches to measuring on-shelf availability have significant limitations:
POS Data Analysis
Point-of-sale data is commonly used to infer out-of-stocks through "zero sales" periods:
Limitations:
- Cannot distinguish between low demand and actual out-of-stocks
- Provides delayed insights rather than real-time alerts
- Often available only at aggregated levels for brands
- Less accurate for slow-moving items
Perpetual Inventory Systems
These systems track theoretical inventory levels based on recorded deliveries and sales:
Limitations:
- Studies show 32-45% inaccuracy rates
- Cannot account for theft, damage, or misplacement
- Do not reflect actual shelf conditions
- Require perfect execution of all inventory movements
Manual Audits
Physical checks by store staff or third-party auditors:
Limitations:
- Labor-intensive and expensive
- Provide only periodic snapshots rather than continuous monitoring
- Subject to human error and inconsistency
- Difficult to scale across large store networks
The Technology Solution: Computer Vision and AI
Advanced image recognition technology offers a transformative approach to monitoring on-shelf availability:
How It Works:
- Image Capture: Cameras mounted on shelves, ceilings, or carried by staff capture images of retail shelves
- Image Processing: AI algorithms analyze these images to identify products and shelf conditions
- Data Extraction: The system extracts information about product presence, positioning, and compliance
- Alert Generation: Real-time notifications highlight out-of-stock situations for immediate action
- Analytics: Historical data analysis identifies patterns and optimization opportunities
Key Advantages:
- Real-Time Visibility: Continuous monitoring rather than periodic checks
- Objective Assessment: Consistent, accurate detection without human bias
- Comprehensive Coverage: Monitoring of all products and shelves
- Actionable Insights: Immediate alerts enable prompt replenishment
- Historical Analysis: Trend identification for systemic improvements
Implementation Considerations
Organizations implementing computer vision for on-shelf availability should consider:
- Infrastructure Requirements: Camera placement, networking, and processing capabilities
- Integration Needs: Connections with existing inventory and replenishment systems
- Staff Training: Preparing teams to respond to alerts and use the system effectively
- ROI Calculation: Balancing implementation costs against expected benefits
- Phased Approach: Starting with high-impact categories or problem areas
The most successful implementations typically begin with clearly defined objectives and measurable success criteria.
Collaborative Approach
Improving on-shelf availability requires collaboration between retailers and manufacturers:
- Shared Data: Transparent information exchange about inventory and forecasts
- Joint Planning: Collaborative promotional planning to prevent availability issues
- Aligned Incentives: Mutual recognition of OSA importance for both parties
- Coordinated Response: Clear protocols for addressing out-of-stock situations
This collaborative approach recognizes that both parties have a stake in ensuring products are available when and where consumers want to purchase them.
Conclusion
On-shelf availability remains a critical challenge for retailers and manufacturers, with significant implications for sales, customer satisfaction, and competitive positioning. Traditional measurement methods have proven inadequate for addressing this challenge effectively.
Computer vision and AI technologies offer a transformative solution by providing continuous, accurate monitoring of shelf conditions. These technologies enable retailers and manufacturers to identify and address availability issues in real-time, improving the shopping experience and capturing previously lost sales.
As these technologies continue to evolve and become more accessible, they will play an increasingly important role in helping retailers optimize their operations and remain competitive in a challenging marketplace. For retailers seeking to improve the in-store experience and maximize sales, addressing on-shelf availability through advanced technology is becoming not merely an option but a necessity.
This article provides a historical perspective on on-shelf availability challenges. While Visionify now specializes in computer vision solutions for various industries, we recognize the continuing importance of visual monitoring technologies in retail inventory management.
Want to learn more?
Discover how our Vision AI safety solutions can transform your workplace safety.
Schedule a DemoSchedule a Meeting
Book a personalized demo with our product specialists to see how our AI safety solutions can work for your business.
Choose a convenient time
Select from available slots in your timezone
30-minute consultation
Brief but comprehensive overview of our solutions
Meet our product experts
Get answers to your specific questions
Related Articles
Subscribe to our newsletter
Get the latest safety insights and updates delivered to your inbox.