Machine Vision to Optimize Package Wrapping
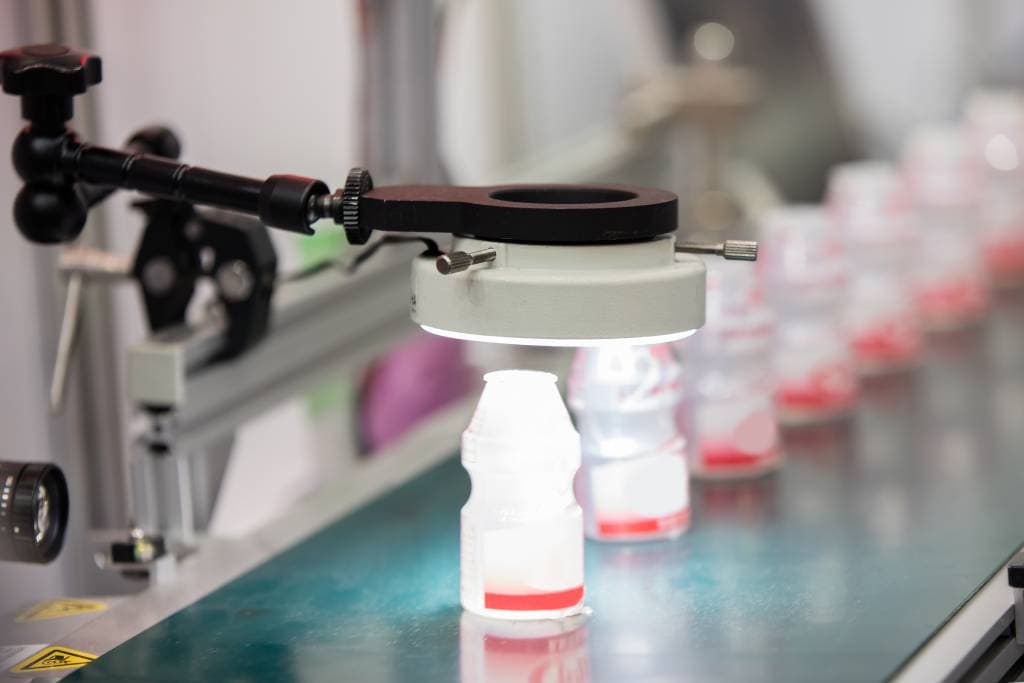
Key Takeaways
- Market Growth: The machine vision market is expected to reach $16.55 billion by 2027
- Packaging Efficiency: Vision systems optimize wrapping to eliminate wasted space and prevent damage
- Quality Assurance: Automated inspection ensures packaging meets standards before shipment
- Advanced Technologies: 3D imaging and deep learning enhance packaging verification capabilities
- Error Reduction: Machine vision significantly reduces human error in packaging processes
The Evolution of Packaging Automation
Machine vision technology has expanded far beyond basic quality control to become an integral part of the production and packaging process itself. According to Brand Essence Research, the machine vision market is valued at $10.79 billion in 2020 and is expected to reach $16.55 billion by 2027, with packaging applications driving significant growth.
Modern packaging operations face increasing demands for accuracy, efficiency, and quality assurance. Machine vision systems address these challenges by automating inspection processes, optimizing package wrapping, and ensuring consistent quality across high-volume production lines.
Vision Sensor Technology in Packaging
Vision sensors represent the foundation of machine vision packaging applications. These specialized devices capture and analyze visual information to verify packaging integrity and identify defects.
Components and Capabilities
Modern vision sensor systems typically include:
- Illumination Sources: Specialized LED lighting to highlight package features
- Image Capture Devices: High-resolution cameras optimized for production environments
- Processing Units: Dedicated hardware for real-time image analysis
- Software Algorithms: Specialized code for detecting specific packaging issues
These systems can detect a wide range of packaging problems, including:
- Misaligned Labels: Ensuring proper label placement and orientation
- Seal Integrity: Verifying that packages are properly sealed
- Code Verification: Confirming barcodes and date codes are correct and readable
- Completeness Checks: Ensuring all package components are present
Working Procedure
The vision inspection process follows a systematic approach:
- Illumination: The package is illuminated under controlled lighting conditions
- Image Capture: High-resolution cameras capture detailed images of the package
- Image Processing: Software analyzes the images for defects or irregularities
- Decision Making: The system determines whether the package meets quality standards
- Action: Defective packages are flagged or automatically removed from the production line
This automated approach ensures consistent inspection without the limitations of human visual inspection.
3D Product and Packaging Inspection
While traditional 2D vision systems remain valuable, 3D inspection technologies offer enhanced capabilities for complex packaging applications.
Advantages of 3D Inspection
Three-dimensional inspection systems provide several benefits:
- Volume Measurement: Accurately calculating product volume and fill levels
- Surface Analysis: Detecting subtle deformations in package surfaces
- Depth Perception: Identifying issues not visible in 2D images
- Comprehensive Inspection: Examining packages from multiple perspectives simultaneously
Implementation Approach
Modern 3D inspection systems typically employ:
- Laser Triangulation: Projecting laser lines to create detailed surface maps
- Structured Light: Using patterned light to generate 3D models
- Stereo Vision: Employing multiple cameras to create depth perception
- Time-of-Flight: Measuring the time for light to reflect from surfaces
These technologies enable manufacturers to verify package integrity with unprecedented accuracy, even when products are partially obscured or in complex arrangements.
Deep Learning for Packaging Verification
Artificial intelligence, particularly deep learning, has transformed packaging inspection capabilities.
Classification and Verification
Deep learning models excel at:
- Package Classification: Identifying different product types and variants
- Defect Detection: Recognizing subtle quality issues that traditional systems might miss
- Contextual Understanding: Accounting for variations in lighting, orientation, and position
- Anomaly Detection: Identifying unusual or unexpected packaging conditions
Training and Implementation
Implementing deep learning for packaging verification involves:
- Data Collection: Gathering images of both acceptable and defective packages
- Model Training: Teaching the system to recognize patterns and anomalies
- Validation: Testing the model against known examples to ensure accuracy
- Deployment: Integrating the trained model into the production environment
- Continuous Improvement: Refining the model based on new data and feedback
This approach enables packaging systems to improve over time, adapting to new products and identifying emerging quality issues.
Assembly Verification with Machine Vision
Package assembly verification ensures that all components are correctly positioned and secured before shipment.
Key Applications
Machine vision excels at verifying:
- Component Presence: Confirming all required items are included
- Proper Positioning: Ensuring components are correctly oriented
- Seal Integrity: Verifying packages are properly sealed
- Label Placement: Confirming labels are correctly positioned and readable
Implementation Challenges
Effective assembly verification must overcome several challenges:
- Product Variability: Accommodating different package sizes and configurations
- Speed Requirements: Maintaining accuracy at production line speeds
- Environmental Factors: Adapting to changing lighting and vibration conditions
- Mixed Product Handling: Identifying and verifying different product types simultaneously
Advanced machine vision systems address these challenges through sophisticated algorithms, flexible lighting, and robust hardware designs.
Implementation Considerations
Organizations implementing machine vision for packaging applications should consider:
- Integration Requirements: How the vision system will connect with existing packaging equipment
- Speed and Throughput: Ensuring the system can keep pace with production requirements
- Flexibility: Accommodating different package types and product variations
- Maintenance Needs: Planning for system calibration and updates
- Return on Investment: Calculating cost savings from reduced errors and improved efficiency
The most successful implementations typically start with clearly defined objectives and expand capabilities over time.
Conclusion
Machine vision technology has transformed packaging operations, enabling manufacturers to optimize wrapping processes, verify package integrity, and ensure consistent quality. As these technologies continue to advance, particularly in 3D imaging and artificial intelligence, packaging operations will achieve even higher levels of efficiency, accuracy, and reliability.
For manufacturers seeking to improve packaging quality while reducing costs, machine vision represents not merely a technological upgrade but a strategic investment in operational excellence and customer satisfaction.
This article provides a historical perspective on machine vision in packaging. While Visionify now specializes in computer vision solutions for various industries, we recognize the continuing importance of visual inspection technologies in ensuring packaging quality and efficiency.
Want to learn more?
Discover how our Vision AI safety solutions can transform your workplace safety.
Schedule a DemoSchedule a Meeting
Book a personalized demo with our product specialists to see how our AI safety solutions can work for your business.
Choose a convenient time
Select from available slots in your timezone
30-minute consultation
Brief but comprehensive overview of our solutions
Meet our product experts
Get answers to your specific questions
Related Articles
Subscribe to our newsletter
Get the latest safety insights and updates delivered to your inbox.