A Beginner's Guide to Factory Vision
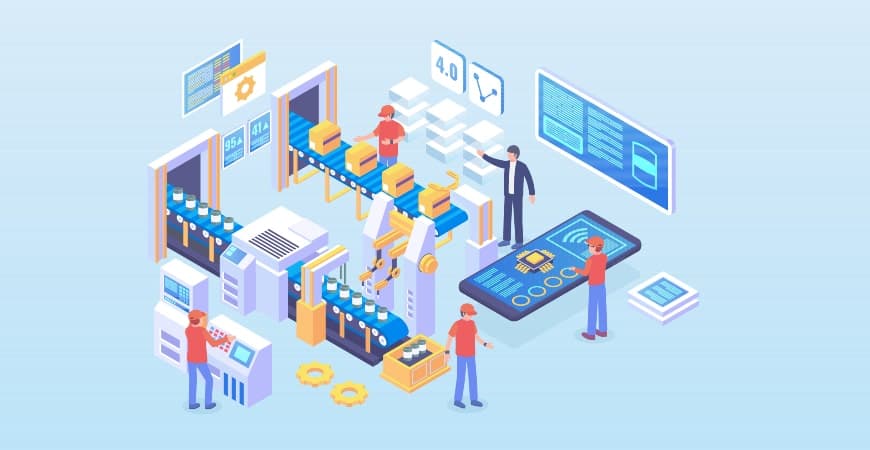
Key Takeaways
- Quality Assurance: Factory vision systems automate inspection processes to ensure consistent product quality
- Efficiency Gains: Visual monitoring identifies bottlenecks and optimizes production flow
- Error Reduction: Early detection of defects minimizes waste and rework
- Implementation Flexibility: Solutions can be scaled from simple manual systems to fully automated inspection
- ROI Potential: Properly implemented systems deliver measurable returns through improved quality and reduced costs
Understanding Factory Vision
Factory vision refers to the use of visual monitoring and inspection technologies to oversee manufacturing processes. These systems combine cameras, lighting, software, and often artificial intelligence to detect defects, verify assembly, and ensure quality standards are consistently met throughout production.
Modern factory vision systems combine cameras, specialized lighting, and AI-powered software
At its core, factory vision serves as the "eyes" of the production process, continuously monitoring operations that would be impossible for human inspectors to track with the same level of consistency and precision. This technology has become a cornerstone of Industry 4.0 initiatives, enabling smarter, more responsive manufacturing environments.
How Factory Vision Works
Factory vision systems typically include several key components:
1. Image Capture
The process begins with capturing visual information through:
- Industrial Cameras: Specialized cameras designed for manufacturing environments
- Lighting Systems: Controlled illumination to highlight features and defects
- Positioning Equipment: Ensuring consistent image capture angles and distances
2. Image Processing
Once captured, images are analyzed through:
- Edge Detection: Identifying object boundaries and features
- Pattern Matching: Comparing products against reference images
- Color Analysis: Verifying correct coloration and finishes
- Dimensional Measurement: Ensuring products meet size specifications
3. Decision Making
Based on analysis results, the system makes determinations:
- Pass/Fail Decisions: Accepting or rejecting products based on quality standards
- Sorting Commands: Directing products to appropriate handling systems
- Process Feedback: Providing data to adjust upstream manufacturing processes
- Documentation: Recording inspection results for quality assurance records
4. Integration
Factory vision systems connect with broader manufacturing infrastructure:
- PLC Integration: Communicating with programmable logic controllers
- MES Connection: Feeding data to manufacturing execution systems
- ERP Reporting: Providing quality metrics to enterprise resource planning systems
- Robotics Control: Guiding automated handling and assembly systems
This integration enables not just inspection but comprehensive process control and optimization.
Key Applications in Manufacturing
Factory vision systems serve numerous functions in production environments:
Quality Control
- Defect Detection: Identifying surface flaws, missing components, or assembly errors
- Dimensional Verification: Ensuring products meet size and shape specifications
- Color Inspection: Verifying correct coloration and finishes
- Label Verification: Confirming proper labeling and packaging
Process Monitoring
- Assembly Verification: Ensuring all components are correctly installed
- Sequence Checking: Verifying manufacturing steps occur in proper order
- Tool Monitoring: Detecting worn or damaged production tools
- Material Tracking: Following components through the production process
Safety and Compliance
- Foreign Object Detection: Identifying contamination or unwanted materials
- Regulatory Compliance: Documenting quality processes for regulatory requirements
- Worker Safety: Monitoring hazardous areas without human presence
- Environmental Monitoring: Tracking emissions or waste products
These applications demonstrate the versatility of factory vision across manufacturing sectors.
Implementation Approaches
Organizations can implement factory vision at various levels of sophistication:
1. Basic Visual Inspection
- Manual Camera Systems: Operators use camera-assisted visual inspection
- Simple Pass/Fail Checks: Basic verification of product characteristics
- Spot Checking: Sampling products rather than 100% inspection
- Documentation Focus: Creating visual records of production
This approach offers improved quality control with minimal investment.
2. Automated Inspection Cells
- Dedicated Inspection Stations: Purpose-built inspection points in the production line
- Automated Image Capture: Consistent imaging without operator intervention
- Software-Based Analysis: Computerized evaluation of product characteristics
- Rejection Mechanisms: Automatic removal of defective products
This level provides consistent inspection without disrupting production flow.
3. Integrated Vision Systems
- Line-Wide Implementation: Vision systems throughout the production process
- Real-Time Feedback: Immediate process adjustments based on inspection results
- Data Integration: Connection with broader manufacturing systems
- Predictive Capabilities: Identifying trends before they cause quality issues
Fully integrated systems deliver comprehensive quality control and process optimization.
Implementation Considerations
When implementing factory vision, organizations should consider:
- Application Requirements: Clearly define what needs to be inspected and why
- Environmental Factors: Lighting, vibration, dust, and other conditions affecting image capture
- Production Speed: Ensuring the system can keep pace with manufacturing throughput
- Integration Needs: How the vision system will connect with existing equipment
- ROI Expectations: Realistic assessment of cost savings and quality improvements
Successful implementations typically start with well-defined, high-impact applications before expanding to broader coverage.
Measuring Success
The effectiveness of factory vision systems can be measured through several metrics:
- Defect Reduction: Decrease in customer complaints and returns
- Scrap Reduction: Less waste from rejected products
- Throughput Improvement: Increased production speed with maintained quality
- Labor Efficiency: Reallocation of inspection personnel to value-added tasks
- Warranty Cost Reduction: Fewer field failures and warranty claims
These metrics help justify investment and guide system refinement.
Getting Started with Factory Vision
For organizations new to factory vision, consider these steps:
- Identify Critical Quality Points: Determine where inspection would add the most value
- Start Small: Implement a pilot project focused on a specific inspection need
- Measure Results: Document improvements in quality, efficiency, and cost
- Build Expertise: Develop internal knowledge of vision system capabilities
- Expand Strategically: Add capabilities based on demonstrated success
This measured approach minimizes risk while building organizational capability.
Conclusion
Factory vision systems represent a powerful tool for manufacturing quality and efficiency. By providing consistent, objective inspection throughout the production process, these systems help organizations reduce defects, minimize waste, and improve overall productivity.
As manufacturing continues to evolve toward greater automation and intelligence, factory vision will play an increasingly central role in ensuring product quality while optimizing production processes. For organizations seeking to remain competitive in demanding markets, implementing appropriate vision technology is becoming not merely an option but a necessity.
This article provides a historical perspective on factory vision systems. While Visionify now specializes in computer vision solutions for various industries, we recognize the continuing importance of visual inspection technologies in manufacturing environments.
Want to learn more?
Discover how our Vision AI safety solutions can transform your workplace safety.
Schedule a DemoSchedule a Meeting
Book a personalized demo with our product specialists to see how our AI safety solutions can work for your business.
Choose a convenient time
Select from available slots in your timezone
30-minute consultation
Brief but comprehensive overview of our solutions
Meet our product experts
Get answers to your specific questions
Related Articles
Subscribe to our newsletter
Get the latest safety insights and updates delivered to your inbox.