How to Achieve Direct Part Mark Code Quality?
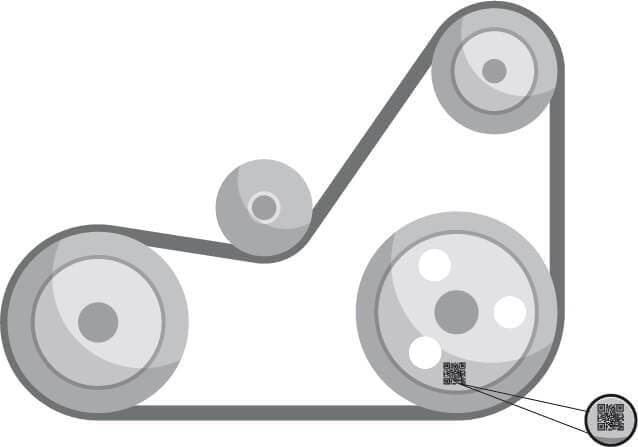
Key Takeaways
- Permanent Identification: DPM codes provide durable, permanent identification that survives harsh environments
- Quality Challenges: Surface variations, material properties, and marking methods all affect code quality
- Critical Applications: Industries like automotive, aerospace, and medical devices rely on DPM for safety and compliance
- Verification Importance: Proper verification ensures codes remain readable throughout product lifecycle
- Lighting Techniques: Specialized lighting approaches are essential for accurate DPM verification
Understanding Direct Part Marking
Direct Part Marking (DPM) is a process of permanently marking parts with machine-readable codes for identification and traceability. Unlike labels or tags that can fall off or deteriorate, DPM creates marks directly on the component surface that remain readable throughout the product's lifecycle.
Common DPM methods include:
- Laser Etching: Using focused laser beams to alter surface material
- Dot Peening: Creating a pattern of small indentations with a stylus
- Chemical Etching: Using chemicals to remove material in a controlled pattern
- Inkjet Printing: Applying specialized inks directly to parts
These marks typically contain Data Matrix codes, which can store substantial information in a small space and offer error correction capabilities. Industries including automotive, aerospace, electronics, and medical devices rely on DPM for component tracking, quality control, and counterfeit prevention.
The DPM Quality Challenge
Direct part marking presents unique quality challenges not found with traditional printed labels:
1. Permanence Requirements
Unlike labels that can be reprinted if quality is poor, DPM codes are permanent:
- Once applied, they cannot be easily corrected
- Poor quality marks may render parts unusable
- Rework is often impossible or prohibitively expensive
2. Environmental Considerations
DPM codes must survive harsh conditions:
- Exposure to oils, solvents, and chemicals
- Extreme temperatures during manufacturing processes
- Abrasion and wear during normal use
- Cleaning procedures and sterilization (for medical devices)
3. Surface Variations
Components requiring DPM often have challenging surfaces:
- Curved or irregular geometries
- Highly reflective materials like polished metal
- Textured or granular surfaces
- Varying colors and finishes
4. Size Constraints
Many applications require extremely small codes:
- Miniature electronic components
- Space-limited medical devices
- Densely packed assemblies
These factors combine to make DPM quality significantly more challenging than traditional barcode printing, requiring specialized approaches to both marking and verification.
Critical Quality Factors
Several key factors determine DPM code quality and readability:
1. Cell Formation
- Consistency: Uniform size and shape of individual cells
- Position Accuracy: Correct placement of each cell within the code
- Edge Definition: Clear boundaries between cells
2. Contrast
- Light/Dark Differentiation: Sufficient difference between marked and unmarked areas
- Background Interference: Minimizing patterns or textures that could confuse readers
- Reflectivity Management: Controlling specular reflection from shiny surfaces
3. Quiet Zone
- Clear Border: Maintaining adequate space around the code
- Surface Uniformity: Consistent background in the quiet zone area
4. Code Size
- Module Dimensions: Appropriate cell size for the application
- Overall Proportions: Maintaining correct aspect ratio
Verification: The Key to Quality
Given the challenges and permanence of DPM codes, verification is not optional—it's essential. Proper verification:
- Confirms codes meet quality standards before parts enter service
- Provides objective measurement against international standards
- Predicts readability throughout the product lifecycle
- Identifies specific quality issues for process improvement
Verification Standards
DPM verification typically follows these standards:
- ISO/IEC 15415: General 2D code quality verification
- ISO/IEC TR 29158 (AIM DPM): Specific guidelines for direct part marks
- Industry-Specific Standards: Additional requirements for automotive, aerospace, medical, etc.
These standards define specific parameters to measure and grade, resulting in an overall quality score typically expressed as a letter grade (A through F) or numeric value.
Specialized Verification Techniques
DPM verification requires specialized approaches not needed for traditional barcode verification:
1. Advanced Lighting
The most critical element in DPM verification is appropriate lighting:
- 30° Angle Lighting: Highlights marks on curved or reflective surfaces
- 45° Angle Lighting: Standard for many applications
- 90° Angle Lighting: Direct illumination for certain surface types
- Dome Lighting: Diffuse illumination that minimizes reflections
- Multi-Angle Analysis: Combining results from different lighting approaches
2. Image Processing
Specialized algorithms help extract code information from challenging images:
- Contrast Enhancement: Amplifying subtle differences between cells
- Noise Reduction: Filtering out surface texture and irregularities
- Edge Detection: Identifying cell boundaries in low-contrast situations
- 3D Analysis: Evaluating depth information for dot-peened marks
3. Calibration
Proper calibration ensures accurate measurements:
- Known Reference Standards: Calibrating against certified test cards
- Material-Specific Settings: Adjusting for different surface properties
- Regular Recalibration: Maintaining accuracy over time
Implementation Best Practices
To achieve consistent DPM quality, manufacturers should follow these best practices:
1. Process Development
- Material Testing: Evaluate marking methods on actual production materials
- Parameter Optimization: Determine optimal settings for each marking method and material
- Validation Protocol: Establish formal validation procedures
2. Equipment Selection
- Appropriate Marking Technology: Choose marking methods suited to the application
- Verification Equipment: Invest in proper verification systems with appropriate lighting
- Integration Capabilities: Ensure marking and verification systems can communicate
3. Quality Control
- 100% Verification: Verify every mark, not just samples
- Process Monitoring: Track quality trends to detect gradual degradation
- Failure Analysis: Investigate and address root causes of quality issues
4. Training
- Operator Training: Ensure staff understand DPM quality requirements
- Interpretation Skills: Develop ability to interpret verification results
- Troubleshooting Procedures: Establish clear protocols for addressing quality issues
Conclusion
Direct part marking provides invaluable traceability benefits for manufacturing, but only when codes maintain consistent readability throughout the product lifecycle. The permanent nature of these marks makes quality verification not merely important but essential.
By understanding the unique challenges of DPM, implementing appropriate verification methods, and following industry best practices, manufacturers can achieve the high-quality marks needed for reliable identification in even the most demanding applications.
For industries where component traceability impacts safety, compliance, and quality, investing in proper DPM verification is not an optional expense but a fundamental requirement for responsible manufacturing.
This article provides a historical perspective on direct part marking quality. While Visionify now specializes in computer vision solutions for various industries, we recognize the continuing importance of component traceability and identification in manufacturing environments.
Want to learn more?
Discover how our Vision AI safety solutions can transform your workplace safety.
Schedule a DemoSchedule a Meeting
Book a personalized demo with our product specialists to see how our AI safety solutions can work for your business.
Choose a convenient time
Select from available slots in your timezone
30-minute consultation
Brief but comprehensive overview of our solutions
Meet our product experts
Get answers to your specific questions
Related Articles
Subscribe to our newsletter
Get the latest safety insights and updates delivered to your inbox.