How Industry 4.0 Accelerates Growth in the Manufacturing Sector
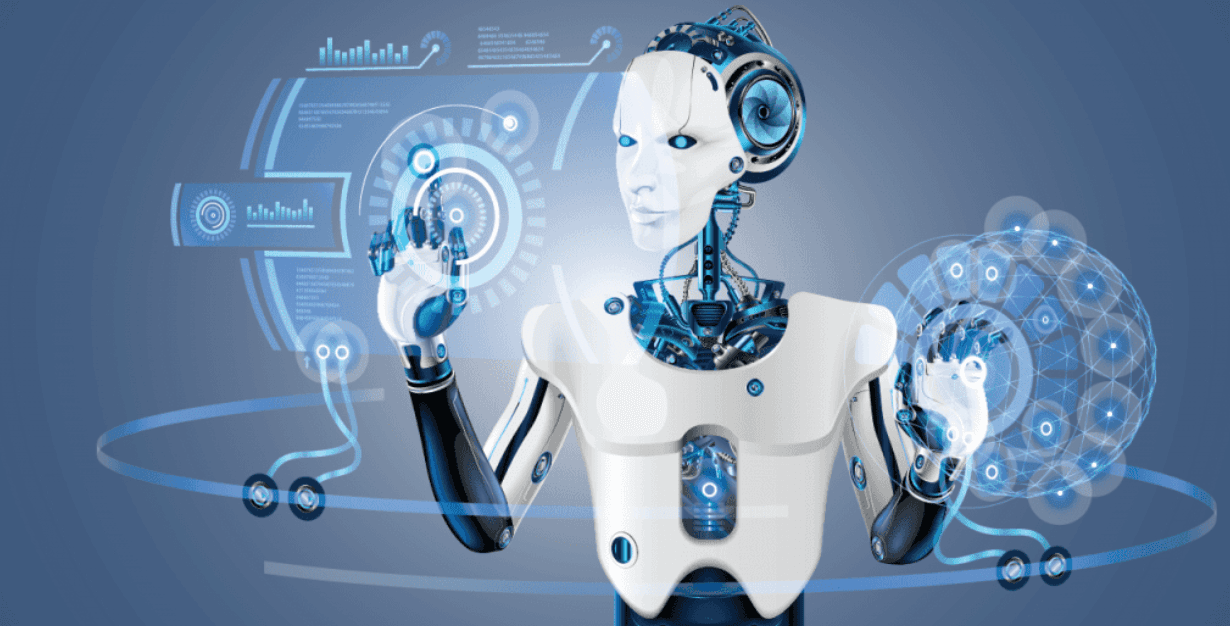
Industry 4.0 represents the fourth industrial revolution—a digital transformation that is fundamentally changing how manufacturers operate through the integration of smart technology, data analytics, and interconnected systems. This revolution is creating unprecedented opportunities for growth, efficiency, and innovation across the manufacturing sector.
The Digital Manufacturing Ecosystem
At its core, Industry 4.0 is an information-intensive, networked production system that connects physical machinery with digital technologies. This integration creates smart factories where equipment, systems, and people communicate seamlessly, enabling real-time decision making and autonomous operations.
The global Industry 4.0 market is projected to reach $219.8 billion by 2026, according to Report Linker, highlighting the significant investment and growth in this transformative approach to manufacturing.
Key Technologies Driving Manufacturing Growth
Digital Work Instructions
Digital work instructions provide operators with interactive, multimedia guidance for complex manufacturing processes. These systems replace traditional paper manuals with dynamic content that can include videos, 3D models, and step-by-step visual guides.
By digitizing work instructions, manufacturers ensure consistent quality, reduce training time, and enable less experienced workers to perform complex tasks with precision. This technology is particularly valuable for specialized processes like deburring, where technique significantly impacts product quality.
Industrial Internet of Things (IIoT)
IIoT connects machines, sensors, and systems to create a continuous flow of operational data. This connectivity enables digital performance management (DPM), where analytics and real-time monitoring drive process improvements.
With IIoT, manufacturers gain visibility into every aspect of their operations, from machine performance to energy consumption. This data-driven approach allows for predictive maintenance, optimized production scheduling, and rapid response to changing conditions.
The IIoT market in manufacturing alone is expected to grow from $27.76 billion in 2018 to $136.83 billion by 2026, according to Fortune Business Insights.
Augmented Reality for Operator Assistance
Augmented reality (AR) overlays digital information onto the physical environment, providing operators with contextual guidance for complex tasks. This technology enables workers to visualize instructions, access technical data, and receive expert assistance without shifting focus from their work.
AR is particularly valuable for operating sophisticated machinery where multiple control points must be monitored simultaneously. By projecting critical information directly into the operator's field of view, AR enhances productivity while reducing errors and training requirements.
Advanced Analytics and Automation
Artificial intelligence and machine learning are transforming manufacturing operations through advanced analytics that identify patterns, predict outcomes, and optimize processes. These technologies enable:
- Predictive maintenance that prevents costly downtime
- Quality control systems that detect defects in real-time
- Production optimization that maximizes throughput and efficiency
- Supply chain visibility that reduces inventory costs
Complementing these analytics capabilities, robotic process automation (RPA) streamlines repetitive tasks in manufacturing services, from order processing to quality reporting. This automation reduces errors, accelerates workflows, and allows skilled workers to focus on higher-value activities.
Business Benefits of Industry 4.0
The adoption of Industry 4.0 technologies delivers multiple advantages for manufacturers:
-
Enhanced Collaboration: Connected systems enable seamless communication between teams, suppliers, and customers, regardless of physical location.
-
Proactive Problem Solving: Real-time data and predictive analytics identify potential issues before they impact production.
-
Operational Efficiency: Automated processes, optimized workflows, and predictive maintenance reduce costs and increase productivity.
-
Talent Attraction: Advanced technologies appeal to younger workers seeking innovative environments, helping manufacturers address skills gaps.
Conclusion
Industry 4.0 represents a fundamental shift in manufacturing that extends far beyond automation. By integrating digital technologies throughout operations, manufacturers can achieve unprecedented levels of efficiency, quality, and innovation.
As these technologies continue to evolve, manufacturers who embrace digital transformation will be positioned not just as product makers but as key players in the global digital economy.
This article provides a historical perspective on Industry 4.0 technologies. While Visionify now specializes in computer vision solutions for safety and compliance, we recognize the continuing importance of digital transformation across manufacturing sectors.
Frequently Asked Questions
Find answers to common questions about this topic
Want to learn more?
Discover how our Vision AI safety solutions can transform your workplace safety.
Schedule a DemoSchedule a Meeting
Book a personalized demo with our product specialists to see how our AI safety solutions can work for your business.
Choose a convenient time
Select from available slots in your timezone
30-minute consultation
Brief but comprehensive overview of our solutions
Meet our product experts
Get answers to your specific questions
Subscribe to our newsletter
Get the latest safety insights and updates delivered to your inbox.