How Computer Vision Systems Detect Foreign Objects In Processed Poultry Products?
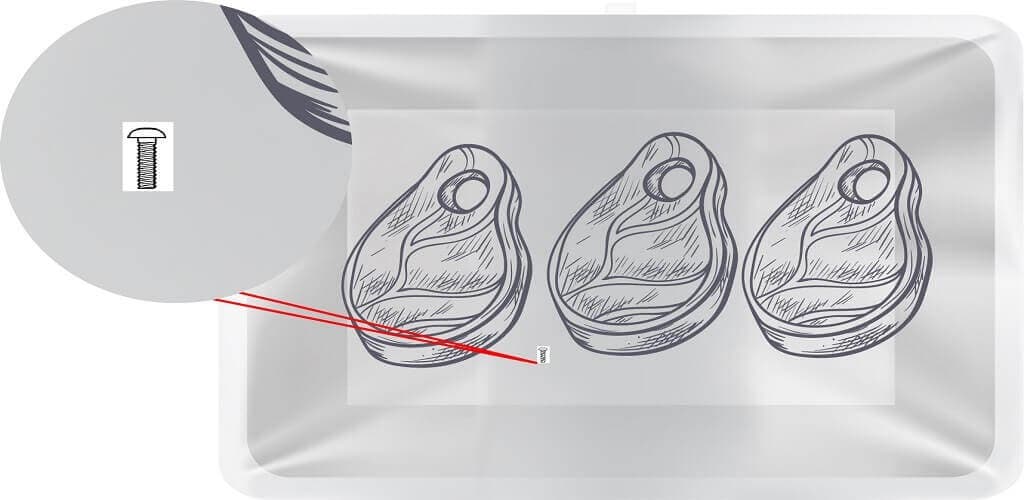
Key Takeaways
- Critical Challenge: Plastic contamination is particularly difficult to detect in poultry products
- High-Speed Processing: Poultry lines move at approximately 12 feet per second (8 mph)
- Beyond Metal Detection: Traditional metal detectors miss plastic, rubber, and other non-metallic contaminants
- Rapid Training: Advanced CV systems can be trained in under an hour with minimal sample data
- Significant Consequences: Contamination incidents lead to costly recalls and brand damage
The Growing Challenge of Foreign Object Contamination
The poultry processing industry faces a significant challenge with foreign object contamination, particularly from plastic fragments. Unlike metal contaminants, which can be detected with traditional metal detectors, plastic pieces are especially problematic because they're difficult to distinguish from the meat itself.
Contamination sources vary widely, including:
- Torn gloves from processing line workers
- Broken pieces of plastic equipment or containers
- Personal items like jewelry
- Packaging materials
- Deliberate contamination incidents
The consequences of missing these contaminants are severe, including expensive recalls, potential consumer injuries, regulatory penalties, and lasting damage to brand reputation.
Foreign objects can be found in crushed candy
Limitations of Traditional Inspection Methods
Conventional approaches to foreign object detection have significant shortcomings:
Manual Inspection
Human inspectors face nearly impossible challenges:
- Processing lines move at approximately 12 feet per second (8 mph)
- Fatigue and attention lapses are inevitable
- Consistent detection of small objects is unreliable
- Labor costs are substantial
Metal Detection
While effective for ferrous and non-ferrous metals, traditional metal detectors:
- Cannot detect plastic, rubber, or glass
- Miss non-conductive foreign materials
- Provide limited protection against the most common contaminants
X-Ray Systems
X-ray technology offers broader detection capabilities but:
- May miss thin plastic pieces
- Has difficulty with contaminants of similar density to the product
- Involves higher implementation and operational costs
Computer Vision: The Next Generation Solution
Advanced computer vision systems address these limitations through sophisticated imaging and artificial intelligence:
How Computer Vision Detection Works
- High-Resolution Imaging: Multiple cameras capture detailed images of products on the processing line
- Multi-Spectral Analysis: Systems may use various light wavelengths to enhance detection
- AI-Powered Recognition: Deep learning algorithms identify anomalies based on color, shape, and texture
- Real-Time Processing: Analysis occurs in milliseconds as products move at high speeds
- Automated Rejection: Contaminated products are automatically removed from the line
Key Advantages of Computer Vision
Computer vision solutions offer several critical benefits:
- Comprehensive Detection: Identifies plastic, rubber, metal, glass, and other foreign materials
- Color Discrimination: Particularly effective with blue plastic (an industry standard for food processing equipment)
- Minimal Training Data: Systems can be trained with relatively few samples
- Rapid Implementation: Operational in hours rather than days or weeks
- Continuous Learning: Performance improves over time as the system processes more products
Implementation Considerations
Poultry processors implementing computer vision foreign object detection should consider:
System Placement
Optimal installation points include:
- After deboning but before packaging
- Following mixing in ground product lines
- Prior to final packaging
Environmental Factors
For maximum effectiveness:
- Consistent lighting conditions must be maintained
- Regular camera cleaning protocols are essential
- Conveyor belts should provide good contrast with potential contaminants
Integration Requirements
Systems should:
- Connect with existing line control systems
- Provide alerts and rejection signals
- Generate documentation for quality assurance records
Measuring Success
Effective foreign object detection systems demonstrate their value through:
- Reduced Customer Complaints: Fewer reported incidents of foreign materials
- Decreased Recall Risk: Lower probability of costly product recalls
- Documented Detection Events: Records of contaminants caught before shipping
- Return on Investment: Typically achieved within 12-18 months through avoided costs
Future Developments
The technology continues to evolve with:
- Enhanced Sensitivity: Detecting increasingly smaller contaminants
- Faster Processing: Accommodating even higher line speeds
- Multi-Function Systems: Combining foreign object detection with other quality checks
- Predictive Analytics: Identifying patterns to prevent contamination at the source
Conclusion
As consumer expectations for food safety rise and regulatory requirements tighten, poultry processors can no longer rely solely on traditional inspection methods. Computer vision technology offers a powerful solution to the persistent challenge of foreign object contamination, particularly for non-metallic materials like plastic.
By implementing these advanced detection systems, processors not only protect consumers and their brands but also gain operational efficiencies that contribute to a compelling return on investment. As the technology continues to advance, computer vision will likely become the standard for comprehensive foreign object detection throughout the poultry industry.
This article provides a historical perspective on foreign object detection technology in poultry processing. While Visionify now specializes in computer vision solutions for various industries, we recognize the continuing importance of visual inspection systems in ensuring food safety.
Frequently Asked Questions
Find answers to common questions about this topic
Want to learn more?
Discover how our Vision AI safety solutions can transform your workplace safety.
Schedule a DemoSchedule a Meeting
Book a personalized demo with our product specialists to see how our AI safety solutions can work for your business.
Choose a convenient time
Select from available slots in your timezone
30-minute consultation
Brief but comprehensive overview of our solutions
Meet our product experts
Get answers to your specific questions
Related Articles
Subscribe to our newsletter
Get the latest safety insights and updates delivered to your inbox.