Case Study: From Reactive to Proactive Safety – How a Chemical Plant Streamlined Workplace Safety using AI

See It In Action
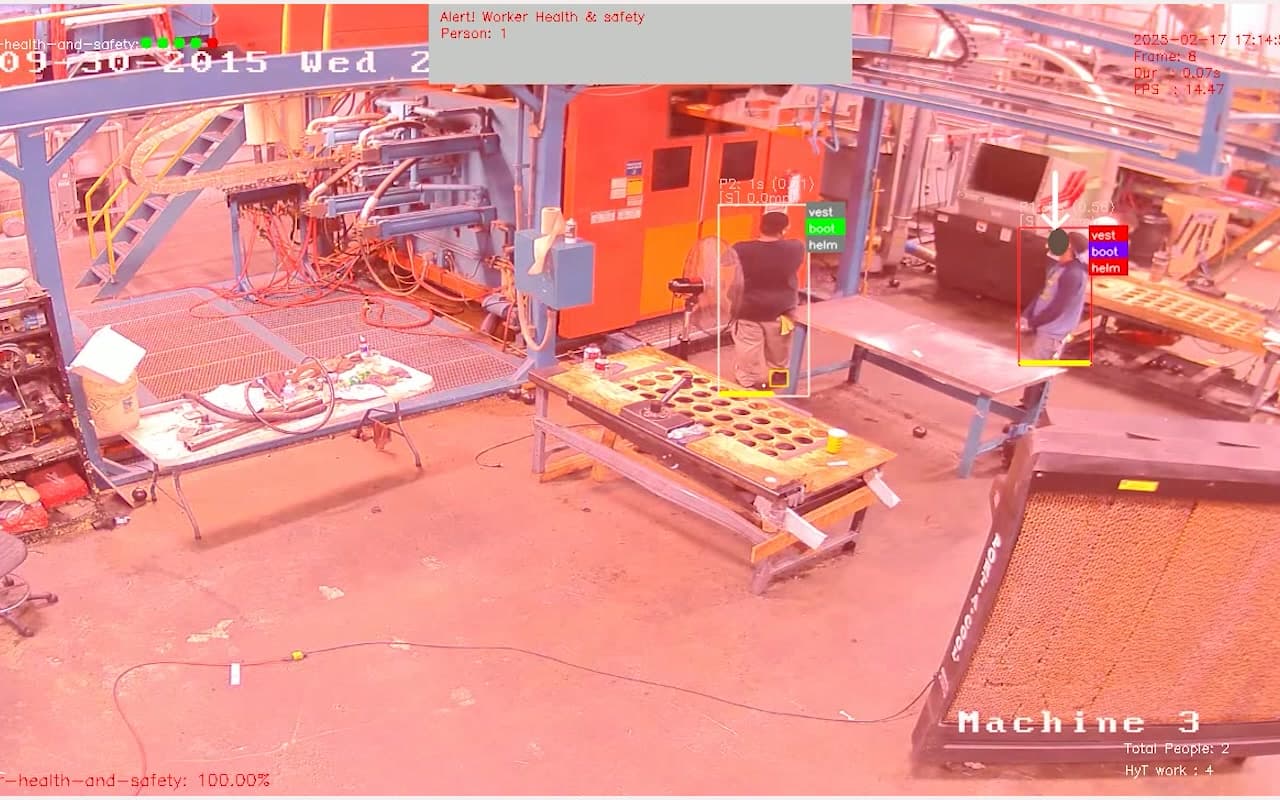
Chemical Plant Safety AI
Demo video showing different safety scenarios deployed at the chemical plant.
Example Videos
Chemical Plant Safety AI
Demo video showing different safety scenarios deployed at the chemical plant.
PPE Compliance in Chemical Environment
Real-time detection of proper PPE usage in hazardous chemical areas
Restricted Area Monitoring
Detection of unauthorized access to high-risk zones and confined spaces
Forklift Safety Monitoring
Prevention of collision incidents between workers and moving forklifts
Key Takeaways
- Rapid Transformation: Shifted from reactive to proactive safety management in just 2 weeks
- No Hardware Investment: Leveraged existing CCTV infrastructure without expensive upgrades
- Significant Safety Improvements: 48% decrease in near-miss incidents and 65% faster hazard response times
- Enhanced Visibility: Over 90% of all incidents in deployed areas automatically logged and reviewed
- Comprehensive Coverage: Implemented 20+ AI safety scenarios addressing specific operational risks
- Real-Time Intervention: Integrated alert system with mobile notifications and on-site alarms
Client Profile
Industry: Chemical Manufacturing
Size: 2,500+ employees across multiple facilities in Texas, USA
Operations: Production of industrial solvents, adhesives, specialty coatings, and chemical products
Our client is a major player in the specialized chemicals manufacturing sector with inherently high-risk operations. Despite maintaining a strong compliance track record and significant investments in employee training, they recognized that traditional safety measures were insufficient to address emerging operational challenges and risks.
The Challenge
Before implementing Vision AI solutions, the client operated with a risk management system that responded only after incidents occurred. Several systemic challenges were apparent:
-
Delayed Incident Detection: Critical incidents like chemical leaks, PPE violations, and near-miss accidents often became apparent only after escalation, causing severe operational and safety consequences
-
Manual Monitoring Limitations: The complex operational environment exceeded the capabilities of human surveillance teams, making it impossible for dedicated safety personnel to effectively monitor the entire operation
-
Static CCTV Systems: Despite having a vast network of CCTV cameras, their surveillance capabilities remained passive—recording footage but providing no real-time risk analytics
-
Unfulfilled Requirements: Off-the-shelf safety analytics software couldn't address the complex and diverse risk scenarios unique to chemical manufacturing, from specialized chemical handling to equipment management
The EHS Director explained: "We had invested heavily in traditional safety protocols, but our ability to prevent incidents rather than react to them was severely limited. We were data-rich but insight-poor, with thousands of hours of surveillance footage that wasn't actively helping us identify risks before they became incidents."
The Solution
After evaluating several workplace safety technology providers, the client partnered with Visionify for their comprehensive Vision AI platform:
1. Out-of-Box AI Scenarios
- Modular, flexible platform with 20+ specialized AI applications
- Each application designed to address specific workplace safety challenges
- Customizable detection parameters for chemical industry-specific risks
- All of Visionify's scenarios can be found at this link: Visionify AI Scenarios.
Intuitive dashboard showing multiple active safety scenarios
2. Seamless Integration
- Direct connection to existing CCTV infrastructure
- No additional hardware investments required
- Preserved existing security investments while adding intelligent analytics
3. Deployed Vision AI Scenarios
- PPE Detection: Real-time monitoring to ensure compliance with critical PPE requirements including gloves, helmets, respirators, and face shields
- Restricted Area Monitoring: Identification and alerting of unauthorized access to confined spaces and other high-risk zones
- Forklift Safety Monitoring: Detection of unsafe proximity between workers and moving forklifts
- Occupancy Monitoring: Tracking the number of individuals in sensitive areas to prevent overcrowding
Mobile safety alerts showing real-time violations and response options
4. Real-Time Alert System
- Automated Mobile Alerts: Safety officers receive instant notifications about risks directly on smartphones and wearable devices
- Integrated Audio Alarms: Floor-level buzzers and audio alarms connected to the detection system for immediate on-ground intervention
- Closed-Loop Response: Complete system from detection to intervention that helps mitigate incidents in real time
Implementation Process
Visionify completed the entire deployment within a remarkably short timeframe:
Phase 1: Assessment & Planning (3 Days)
- Site Survey: Comprehensive evaluation of existing camera infrastructure and operational risk zones
- Use Case Prioritization: Collaborative workshops with EHS teams to identify highest-impact safety scenarios
- Integration Planning: Technical assessment of network capabilities and alert system requirements
Phase 2: Deployment (11 Days)
- Rapid configuration of AI models for selected safety scenarios
- Integration with existing camera infrastructure
- Connection to alert systems (mobile and on-site)
- User training and system validation
Results
Within just one month of deployment, the client experienced significant improvements in safety metrics:
Safety Outcomes
- 48% Decrease in Near-Miss Incidents: Real-time alerts and early intervention proved critical in preventing incidents before escalation
- 65% Faster Hazard Response Time: Automated alerts empowered teams to act swiftly when seconds mattered
- Improved Incident Reporting: Over 90% of all incidents in deployed areas automatically logged and reviewed
- Increased Visibility: Total recorded incidents rose by 120% in the first 2 weeks as previously unnoticed safety issues were captured
Operational Impact
- Reduction in Safety Audit Time: 40% less time spent on manual safety inspections
- Decreased Operational Disruptions: 35% fewer emergency shutdowns due to safety concerns
- Enhanced Regulatory Compliance: Comprehensive documentation of safety initiatives and incident prevention
- Improved Employee Confidence: 87% of surveyed employees reported feeling safer in the workplace
Analytics and Insights
The Vision AI platform provided unprecedented visibility into safety trends:
Comprehensive AI Scenarios for PPE Compliance, Area Controls, Vehicle Controls to keep the site safe
The data revealed several surprising insights:
- Time-of-Day Patterns: 70% of PPE compliance issues occurred during shift transitions
- Location-Specific Risks: Certain production areas consistently showed higher incident rates
- Process Correlation: Specific manufacturing processes had stronger associations with safety violations
- Behavioral Indicators: Early warning signs that often preceded more serious incidents
Implementation Challenges & Solutions
The deployment faced several unique challenges in the chemical manufacturing environment:
-
Hazardous Area Monitoring
- Challenge: Camera placement in areas with potentially explosive atmospheres
- Solution: Utilization of existing intrinsically safe camera infrastructure with remote processing
-
Integration with Legacy Systems
- Challenge: Connecting with older security and EHS management systems
- Solution: Development of custom API connectors and middleware solutions
-
Alert Fatigue Concerns
- Challenge: Worry that too many alerts would lead to desensitization
- Solution: Implementation of tiered alert system with severity-based notifications
-
Privacy Considerations
- Challenge: Employee concerns about constant monitoring
- Solution: Focus on violation detection rather than individual tracking, with clear communication about system purpose
Key Success Factors
Several elements contributed significantly to the project's success:
- Rapid Deployment: Quick implementation maintained momentum and stakeholder enthusiasm
- No Hardware Requirements: Leveraging existing infrastructure minimized disruption and costs
- Flexible Configuration: Ability to adjust detection parameters to match specific operational needs
- Integrated Alerts: Direct connection to intervention systems created immediate value
- Collaborative Approach: Close partnership between Visionify and the client's EHS team
Client Testimonial
"Visionify's Vision AI platform has fundamentally transformed our approach to workplace safety. In just two weeks, we evolved from a reactive model where we'd investigate incidents after they occurred to a proactive system that helps us prevent them entirely. The ability to leverage our existing camera infrastructure meant we could implement quickly without capital expenditure, while the immediate alerts have dramatically reduced our response times. Most importantly, our employees feel the difference—they know hazards will be detected and addressed promptly, creating a much stronger safety culture throughout our operation."
— Michael T., EHS Director
Technology Overview
The Vision AI platform deployed at the client site leverages several advanced technologies:
Computer Vision AI
- Deep learning models optimized for industrial safety detection
- Edge + cloud processing architecture for reliable performance
- High accuracy even in challenging industrial lighting conditions
- Continuous learning capability to improve detection over time
Alert Integration Framework
- Multi-channel notification system (mobile, email, on-site alarms)
- Prioritization algorithms to prevent alert fatigue
- Two-way communication for alert acknowledgment and resolution
- Automated escalation for unaddressed critical alerts
Analytics Engine
- Trend identification across multiple safety parameters
- Correlation analysis between operational factors and safety incidents
- Customizable reporting for different stakeholder needs
- Predictive analytics to identify emerging risk patterns
Looking Ahead: Future Expansion
Building on the success of the initial deployment, the client is planning several expansions:
- Integration with process control systems for automated safety interventions
- Deployment of additional AI scenarios including slip/fall detection and chemical leak identification
- Extension to additional facilities nationwide
- Development of predictive risk models based on collected data
Visionify: Revolutionizing Chemical Industry Safety
Our Vision AI platform provided the client with a transformative approach to workplace safety—moving from reactive incident management to proactive risk prevention. By leveraging existing infrastructure and implementing targeted AI scenarios, Visionify delivered immediate value without disrupting operations.
The client now has unprecedented visibility into safety risks across their operation, with the ability to intervene before incidents occur. This successful partnership demonstrates how Visionify's innovative computer vision solutions can address the unique safety challenges of high-risk chemical manufacturing environments.
Conclusion
This case study illustrates the power of Vision AI to transform safety management in high-risk industrial environments. By providing real-time detection, immediate alerts, and actionable insights, our platform enabled the client to create a significantly safer workplace while improving operational efficiency.
The success of this implementation has positioned the client as a safety innovation leader in the chemical industry, with plans to expand the system to additional facilities. For chemical manufacturers looking to move beyond traditional safety approaches, Visionify proves that AI-powered vision technology can deliver rapid, meaningful improvements without requiring extensive infrastructure investments.
Are you facing similar challenges in managing safety in high-risk environments? Contact Visionify today to learn how our Vision AI platform can transform your approach to workplace safety management.
Frequently Asked Questions
Find answers to common questions about this implementation
Ready to achieve similar results?
Let us show you how our Vision AI safety solutions can transform your workplace safety.
Schedule a ConsultationSchedule a Meeting
Book a personalized demo with our product specialists to see how our AI safety solutions can work for your business.
Choose a convenient time
Select from available slots in your timezone
30-minute consultation
Brief but comprehensive overview of our solutions
Meet our product experts
Get answers to your specific questions