Case Study: Automatic Inline Label Inspection System for Pharmaceutical Packaging
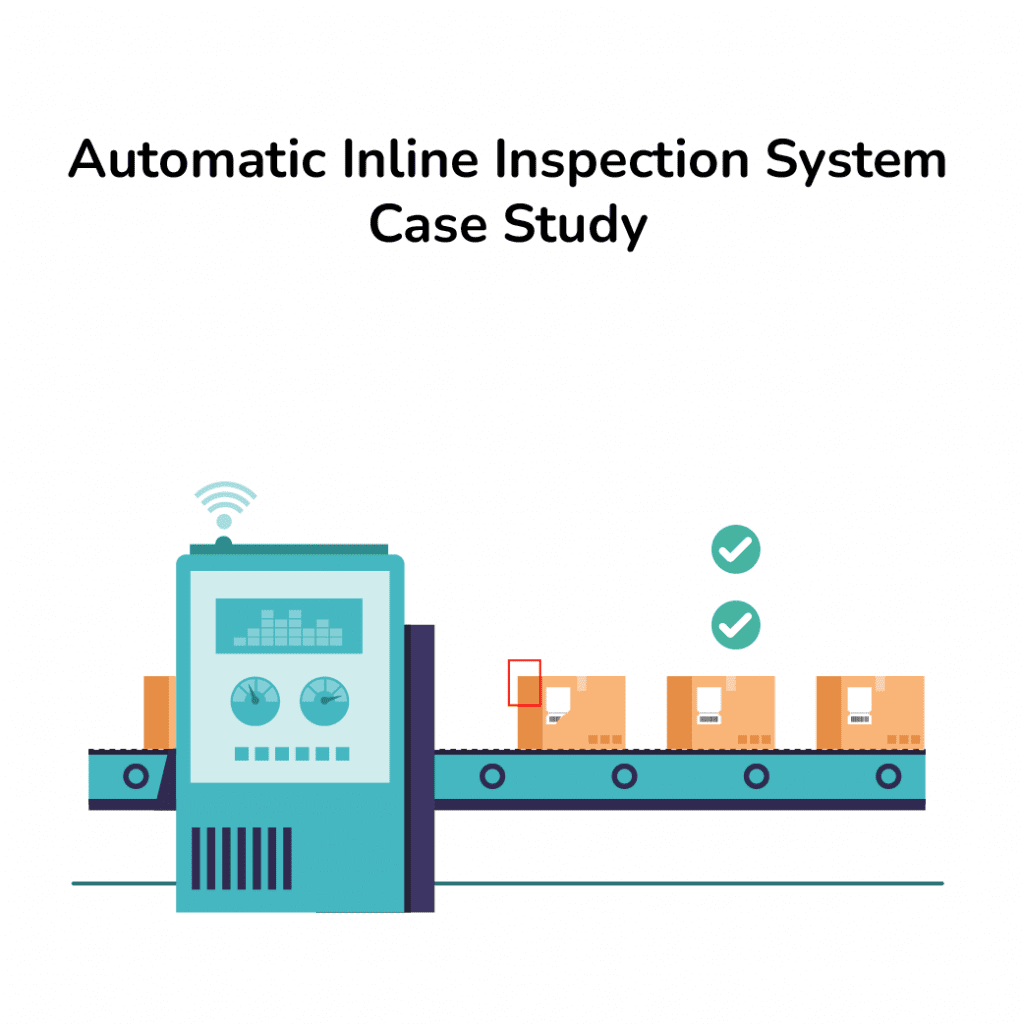
Client Profile
Industry: Pharmaceutical Packaging
Size: Mid-sized packaging company with multiple production facilities
Location: United States
Production Volume: 150+ million labels annually
Our client is a specialized packaging company producing labels, cartons, and inserts for pharmaceutical products. With strict regulatory requirements and zero tolerance for errors in medication packaging, label quality is critical to their business operations and customer relationships.
The Challenge
The client was facing significant challenges with their label inspection process, which had direct implications for product safety and regulatory compliance:
- Zero-Defect Requirement: Pharmaceutical clients demanded 100% defect-free labels for medication packaging.
- Manual Inspection Limitations: Human inspectors could not reliably achieve the required quality levels.
- High Production Speeds: Label printing at high speeds made visual inspection extremely difficult.
- Regulatory Pressure: FDA and other regulatory bodies required comprehensive documentation of quality control.
- Costly Recalls: Mislabeled pharmaceutical products could lead to expensive recalls and potential liability.
- Complex Label Designs: Multiple languages, barcodes, and critical dosage information increased inspection complexity.
The Quality Director explained their situation: "In pharmaceutical packaging, there's absolutely no room for error. A single mislabeled medication can have serious consequences for patient safety and trigger costly recalls. Our manual inspection process simply couldn't provide the level of certainty our clients required, and we needed a solution that could guarantee defect-free labels while maintaining our production speeds."
The Solution
After evaluating several options, the company partnered with Visionify to implement a comprehensive Automatic Inline Label Inspection System across their production facility:
1. High-Performance Imaging System
- Installation of pixel line scan cameras above the exit points of label printers/rewinders
- Custom vision bar lighting system for optimal illumination
- Encoder wheel integration for precise line synchronization
- Real-time image capture and analysis of each label during production
2. Advanced Defect Detection
- Computer vision algorithms specifically trained to identify multiple label issues:
- Missing or incorrect text
- Barcode quality and readability
- Print defects (smudging, fading, streaking)
- Color accuracy and consistency
- Registration and alignment issues
- Machine learning models capable of detecting even subtle defects critical for pharmaceutical applications
3. Multi-Camera Configuration
- Four printers equipped with line scan camera/light/encoder combinations
- Two vision controllers, each managing two cameras
- Distributed processing architecture for high-speed analysis
- Redundant systems to prevent downtime
4. Flexible Management Interface
- User-friendly interface for adding and editing label sets
- Customizable inspection parameters for different pharmaceutical products
- Real-time monitoring and alerting capabilities
- Comprehensive reporting and analytics dashboard
Implementation Process
The implementation followed a structured approach to ensure minimal disruption to production:
-
Assessment & Planning (3 weeks)
- Comprehensive analysis of current labeling and inspection processes
- Identification of optimal inspection points in the production line
- Camera and lighting placement planning
- Development of integration strategy with existing systems
-
Pilot Deployment (4 weeks)
- Installation on one production line
- Initial model training with thousands of label images
- Calibration of detection thresholds and classification parameters
- Side-by-side comparison with manual inspection results
-
System Refinement (3 weeks)
- Analysis of false positives and false negatives
- Additional training to improve detection accuracy
- Fine-tuning of classification thresholds to optimize rejection rates
- Validation against regulatory requirements
-
Full-Scale Implementation (6 weeks)
- Phased rollout across all production lines
- Integration with production management systems
- Comprehensive training for quality control and production staff
- Development of standard operating procedures
-
Continuous Improvement (Ongoing)
- Regular model updates based on new label designs
- Periodic retraining with new production data
- System optimization for different product lines
- Addition of new detection capabilities as needed
Results
After six months of operation, the Automatic Inline Label Inspection System delivered significant improvements across multiple performance metrics:
Quality Improvements
- 99.8% detection accuracy for critical label defects
- Zero defective labels reaching pharmaceutical clients
- Full compliance with FDA and international regulatory requirements
- 100% inspection coverage of all produced labels
Operational Efficiencies
- 32% increase in production throughput
- Inspection capacity matching production speed of up to 250 meters per minute
- 72% reduction in quality control labor costs
- Automated rejection of defective labels without stopping production
- Real-time quality feedback to printing and production teams
Financial Impact
- Annual savings of $580,000 in avoided recalls and rework
- $210,000 decrease in labor costs
- Increased revenue from higher production capacity
- ROI of 315% within the first year
- Payback period of 3.8 months
Additional Benefits
- Regulatory Compliance: Comprehensive documentation for FDA audits
- Enhanced Client Relationships: Ability to guarantee zero-defect deliveries
- Data-Driven Insights: Identification of patterns in defects led to upstream process improvements
- Better Resource Allocation: Quality control staff focused on process improvement rather than routine inspection
- Competitive Advantage: Ability to secure high-value pharmaceutical contracts
Key Success Factors
Several elements were crucial to the project's success:
-
High-Performance Imaging: Line scan technology optimized for high-speed label inspection.
-
Synchronized Inspection: Encoder wheel integration ensured precise timing with production line speed.
-
Customized Lighting: Vision bar illumination designed specifically for pharmaceutical label materials and printing techniques.
-
Flexible Configuration: System architecture that allowed for easy adaptation to different label types and products.
-
User-Friendly Interface: Intuitive controls for adding and editing label sets without requiring technical expertise.
Implementation Challenges & Solutions
The project faced several challenges during implementation:
-
Production Speed
- Challenge: High-speed label production required ultra-fast image capture and processing
- Solution: Implementation of line scan cameras and distributed processing architecture to match production pace
-
Label Variety
- Challenge: Hundreds of different pharmaceutical label designs with critical information
- Solution: Development of a flexible database system with rapid configuration capabilities for different label templates
-
Integration with Existing Equipment
- Challenge: Connecting with diverse printing and rewinding equipment from multiple manufacturers
- Solution: Custom mechanical and electronic interfaces designed for each printer type
-
Validation Requirements
- Challenge: Meeting pharmaceutical industry validation standards for inspection systems
- Solution: Comprehensive validation protocol development and documentation to satisfy regulatory requirements
Client Testimonial
"Visionify's Automatic Inline Label Inspection System has completely transformed our quality assurance process. We've gone from a labor-intensive inspection process with inherent limitations to a fully automated system that catches defects we couldn't even see before. The ability to guarantee zero-defect labels to our pharmaceutical clients has been a game-changer for our business. The system has paid for itself multiple times over through avoided recalls and increased production capacity. The flexibility to easily add and edit label sets has been particularly valuable as we frequently handle new pharmaceutical products with unique requirements."
— Michael S., Director of Quality Assurance
Technology Overview
Our solution leverages several advanced technologies to provide accurate, high-speed label inspection:
Specialized Imaging System
- High-resolution line scan cameras capture detailed images of each label
- Custom vision bar lighting system to highlight printing defects
- Encoder wheel integration for precise synchronization with line speed
- Multi-camera configuration for comprehensive coverage
Advanced Detection Algorithms
- Custom computer vision algorithms trained specifically for pharmaceutical label requirements
- Deep learning models that can detect subtle defects critical for medication safety
- Optical character recognition (OCR) for verifying critical text elements
- Barcode verification to ensure scannable products
Distributed Processing Architecture
- Multiple vision controllers managing multiple cameras
- Edge computing for immediate analysis at the production line
- Parallel processing to handle high-volume image data
- Low-latency decision making for timely rejection of defective labels
Flexible Management System
- Intuitive interface for adding and editing label templates
- Customizable inspection parameters for different pharmaceutical requirements
- Comprehensive reporting and analytics dashboard
- Integration capabilities with enterprise quality management systems
PC-Based vs. Smart Camera Solutions
For this implementation, we recommended and deployed a PC-based vision system due to:
- The high processing demands of pharmaceutical label inspection
- Need for advanced features including OCR and barcode verification
- High production speeds requiring distributed processing
- Complex decision-making algorithms for defect classification
For simpler applications, our smart camera-based solutions provide cost-effective alternatives while maintaining high quality standards. Our technical team assesses each client's specific needs to recommend the optimal solution.
Visionify – Empowering Pharmaceutical Quality Through Vision AI
Our Automatic Inline Label Inspection solution provided our client with powerful tools to overcome their pharmaceutical labeling quality challenges. Through automated detection, intelligent classification, and comprehensive analytics, Visionify not only helped achieve zero-defect production but also enhanced operational efficiency and regulatory compliance.
Our client can now confidently supply labels for critical pharmaceutical products knowing that every label meets the highest quality standards. This successful implementation exemplifies how Visionify's innovative computer vision solutions can transform pharmaceutical packaging quality control through advanced AI technology.
Conclusion
This case study demonstrates how an automatic inline label inspection system can revolutionize quality control in pharmaceutical packaging. By implementing an AI-powered inspection system, our client was able to achieve zero-defect production while increasing throughput and ensuring regulatory compliance.
The success of this implementation has led to the company standardizing the system across all their production facilities and expanding its use to other packaging components including cartons and inserts. The data collected from the system has also provided valuable insights for process improvements that have further enhanced overall production quality.
Are you facing similar labeling challenges in your packaging operations? Contact Visionify today to learn how our Automatic Inline Label Inspection System can transform your approach to product quality and regulatory compliance.
Ready to achieve similar results?
Let us show you how our Vision AI safety solutions can transform your workplace safety.
Schedule a ConsultationRelated Case Studies
Schedule a Meeting
Book a personalized demo with our product specialists to see how our AI safety solutions can work for your business.
Choose a convenient time
Select from available slots in your timezone
30-minute consultation
Brief but comprehensive overview of our solutions
Meet our product experts
Get answers to your specific questions