Why Safety Measurement in Industrial Operations Needs a Digital Overhaul
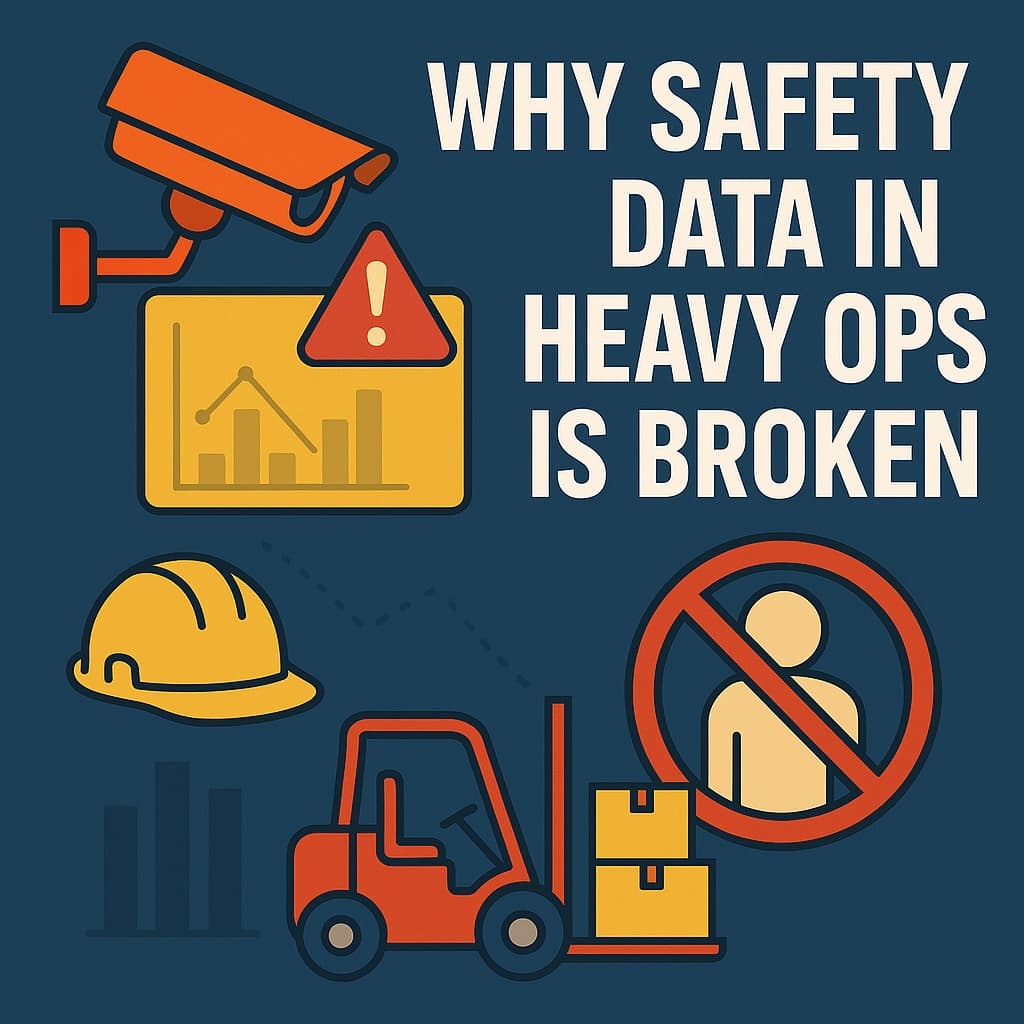
See It In Action
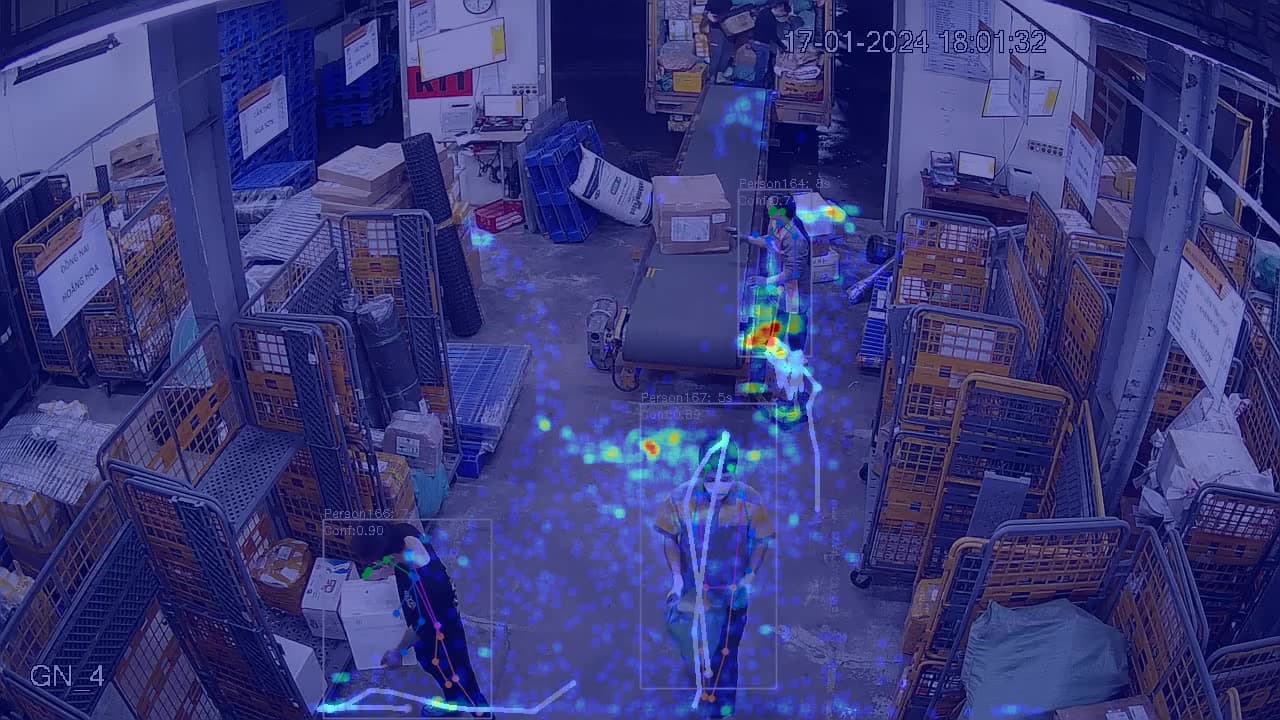
Heatmap Safety AI
Demo of Heatmap Safety AI
Example Videos
Heatmap Safety AI
Demo of Heatmap Safety AI
Forklift Safety AI
How AI predicts and prevents workplace incidents
Detect Smoke and Fire events with AI
How AI detects smoke and fire events in real-time
Key Takeaways
- Data Blind Spots: Up to 50% of serious injuries and 25% of minor incidents go unreported in industrial settings
- Cost Impact: Average workers' compensation claims cost $44,000, making accurate incident tracking crucial
- Measurement Challenges: Traditional methods fail due to human bias, manual processes, and reactive monitoring
- AI Solution: Computer vision and AI can increase incident capture rates by 4-5 times
- ROI Potential: Modern safety systems typically achieve payback in less than 12 months
The Broken State of Safety Data in Heavy Operations
In today's industrial and warehousing operations, safety measurement remains stuck in the analog age. Despite advances in automation and digital transformation, most facilities still rely on a fundamentally flawed system: people noticing incidents, remembering details, and manually typing them into forms. This approach creates dangerous blind spots in safety data that can have serious consequences.
Traditional safety monitoring relies heavily on manual reporting, creating significant data gaps
The scale of underreporting is staggering. According to OSHA estimates, up to 50% of serious workplace injuries go unreported. The National Safety Council's research reveals an even more concerning trend: more than 25% of workers admit they never report minor injuries or near misses. This creates a dangerous disconnect between recorded safety metrics and actual workplace conditions.
Why Incidents Go Unreported
Several factors contribute to this widespread underreporting:
- Human-Reporting Bias: Workers often fear blame or disciplinary action
- Complicated Forms: Lengthy incident reports discourage timely documentation
- Production Pressure: The drive to meet targets can overshadow safety concerns
- Shift Challenges: Night shifts face particular problems with less supervision and increased fatigue
- Near-Miss Neglect: Critical leading indicators disappear from the data lake entirely
The Cost of Flying Blind
Every missing data point in safety measurement represents hidden costs and risks. The National Safety Council's 2021-22 claims data reveals that the average workers' compensation claim costs approximately $44,000. When incidents go unreported, organizations not only miss opportunities to prevent future accidents but also face climbing insurance premiums despite seemingly good safety metrics.
"If half of your incidents never make it into the logbook, your AFR may look world-class while your insurance premium keeps climbing."
Many logistics and industrial firms track standard metrics like AFR (Accident Frequency Rate) and IFR (Incident Frequency Rate), but these numbers are only as reliable as their inputs. The OSHA calculation method — (Incidents × 200,000) / hours worked—assumes complete and accurate reporting, which rarely exists in practice.
Three Structural Challenges in Safety Measurement
1. Incomplete Metrics
Traditional safety scorecards rely heavily on supervisors' write-ups and manual processes that vary from shift to shift. CCTV footage is typically only reviewed after an incident occurs, missing valuable preventive opportunities.
2. Reactive CCTV Monitoring
The current approach to video monitoring is fundamentally flawed:
- One security guard typically monitors 40+ screens
- Human attention span limits effective monitoring after 20 minutes
- 24/7 staffing requirements drive up costs
- Critical incidents can be missed during shift changes or busy periods
3. Hard-to-Prove ROI
Finance departments struggle to justify safety investments because:
- Accident costs are scattered across HR and insurance systems
- Prevention benefits are difficult to quantify
- Traditional metrics don't capture near-misses and potential incidents
- ROI calculations often miss indirect costs like productivity loss
Visionify's Solution: Transforming Cameras into Real-Time Safety Sensors
1. Capturing Missed Near-Misses
Our AI-powered system:
- Automatically detects forklift-pedestrian convergence
- Identifies slip hazards and PPE violations
- Increases incident capture rates by 4-5 times
- Provides real-time alerts for immediate intervention
2. Automated AFR/IFR Calculations
The system:
- Auto-tags safety events
- Integrates with hours-worked data
- Generates live AFR dashboards
- Eliminates manual spreadsheet work
- Creates audit-ready documentation
3. Clear ROI Demonstration
Visionify's built-in cost model:
- Converts prevented claims into dollar savings
- Typically achieves payback in less than 12 months
- Accounts for claims averaging $35,000-$40,000
- Includes indirect cost savings
Typical ROI breakdown showing cost savings vs. investment over 3 years
Want to calculate your potential ROI? Try our interactive ROI calculator to see how much you could save by implementing Visionify's safety solutions.
Overcoming Implementation Challenges
Privacy and Security
Our solution is designed with privacy at its core:
- On-premise edge processing
- Automatic face blurring
- No employee ID storage
- SOC-2 Type 2 compliance
- GDPR-ready architecture
Implementation Strategy
We recommend an incremental approach:
- Start with a single high-risk zone
- Benchmark AFR/IFR reduction
- Demonstrate clear ROI
- Scale across the facility
Roadmap to Digital Safety Excellence
1. Baseline Assessment
- Export 12 months of AFR/IFR data
- Analyze workers' compensation payouts
- Identify high-risk areas
2. Pilot Program
- 3-month deployment in busiest areas
- Focus on loading docks and high-traffic zones
- Measure near-miss detection rates
3. Proof of Value
- Document percentage drop in near-misses
- Calculate dollar value of prevented incidents
- Present clear ROI metrics
4. Full-Scale Implementation
- Expand to all forklift zones
- Integrate with corporate EHS systems
- Establish continuous improvement processes
Conclusion: The Future of Safety Measurement
The industrial sector stands at a critical juncture in safety management. Traditional measurement methods are failing to capture the true state of workplace safety, while modern AI-powered solutions offer a path to comprehensive, real-time safety monitoring. By embracing these technologies, organizations can transform their safety culture, reduce incidents, and achieve measurable ROI—all while protecting their most valuable asset: their people.
Learn more about how our AI-powered safety solutions work and explore our comprehensive range of safety scenarios to see how we can help transform your workplace safety.
Ready to transform your safety measurement approach? Contact Visionify today to learn how our AI-powered solutions can help you achieve accurate, real-time safety monitoring and measurable results.
Frequently Asked Questions
Find answers to common questions about this topic
Want to learn more?
Discover how our Vision AI safety solutions can transform your workplace safety.
Schedule a DemoSchedule a Meeting
Book a personalized demo with our product specialists to see how our AI safety solutions can work for your business.
Choose a convenient time
Select from available slots in your timezone
30-minute consultation
Brief but comprehensive overview of our solutions
Meet our product experts
Get answers to your specific questions
Related Articles
Subscribe to our newsletter
Get the latest safety insights and updates delivered to your inbox.