Everything You Need to Know About Packaging Inspection with Image Recognition
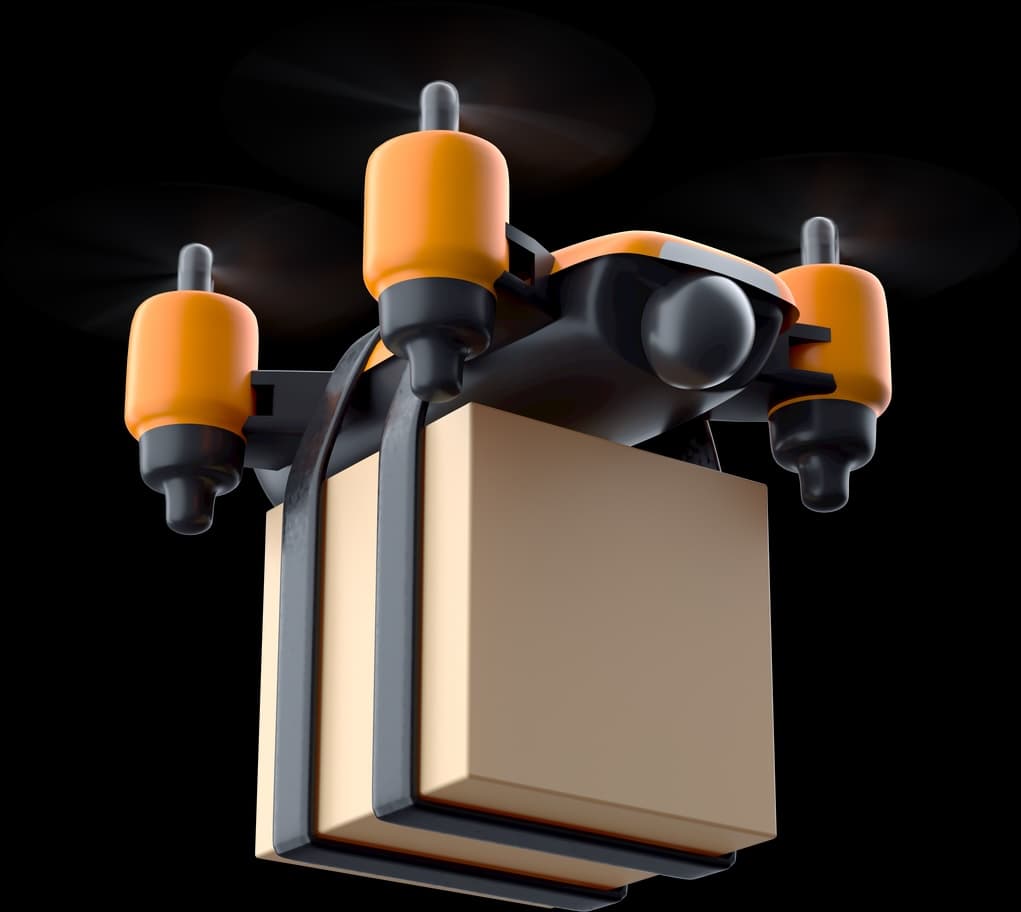
Key Takeaways
- Market Growth: The Global Cargo Inspection Market reached $4.2 billion in 2021
- Critical Function: Package inspection prevents damage, contamination, and brand reputation issues
- AI Revolution: Image recognition technology is transforming traditional inspection processes
- Implementation Path: Successful deployment follows a structured approach from problem definition to continuous improvement
- Multiple Industries: Retail, manufacturing, food, pharmaceutical, and logistics all benefit from automated inspection
Understanding Package Inspection
Package inspection is the systematic examination of products and their packaging before they're shipped to ensure quality standards are met and items remain undamaged throughout the packing process. This critical quality control step is especially important for companies with complex packaging operations or fragile products.
Modern packaging inspection systems combine cameras, lighting, and AI to detect defects
The Importance of Proper Packaging
Packaging serves multiple essential functions that directly impact business success:
Protection
- Prevents damage from physical impacts, vibration, and compression
- Shields products from environmental factors like temperature, humidity, and light
- Protects against contamination from dust, insects, and microorganisms
Brand Experience
- Creates first impressions that influence consumer perception
- Communicates brand values and product benefits
- Differentiates products from competitors in just seconds
Compliance and Safety
- Ensures regulatory requirements are met
- Provides critical information like ingredients, warnings, and usage instructions
- Prevents tampering and maintains product integrity
When packaging fails in any of these areas, the consequences can be severe—from damaged products and returns to regulatory penalties and lost customers.
The Image Recognition Revolution
Traditional package inspection relied heavily on human visual inspection, which is subject to fatigue, inconsistency, and speed limitations. Image recognition technology has transformed this process through:
Automated Visual Analysis
Computer vision systems can examine hundreds of packages per minute with consistent accuracy, far exceeding human capabilities.
Multi-dimensional Inspection
Modern systems can simultaneously check for multiple defect types, including structural damage, label errors, seal integrity, and contamination.
Data-driven Insights
Beyond pass/fail decisions, AI systems generate valuable data about defect patterns that can drive process improvements.
Implementing Image Recognition for Package Inspection
Successful implementation follows a structured approach:
1. Problem Definition
Begin by clearly identifying inspection requirements:
- What specific defects need detection?
- Is real-time inspection needed, or can it be deferred?
- What detection accuracy is required?
- How will the system integrate with existing production lines?
- What notification and reporting capabilities are needed?
2. Data Collection and Preparation
The foundation of any AI system is quality data:
- Gather representative images of both defective and acceptable packages
- Ensure data covers all relevant defect types and variations
- Consider lighting conditions, angles, and production line speeds
- Prepare and annotate images for model training
3. Model Development
Several approaches are available based on requirements and resources:
Pre-built Solutions
Cloud-based machine learning services offer quick implementation but may have limitations for specialized needs.
Pre-trained Models
Existing models can be fine-tuned for specific packaging inspection tasks, balancing development time and customization.
Custom Development
Building models from scratch provides maximum flexibility but requires more time and expertise.
The optimal approach depends on factors like defect complexity, required accuracy, and available resources.
4. Training and Evaluation
Once developed, the model must be trained and rigorously tested:
- Train using the prepared dataset
- Evaluate performance against test data not used in training
- Measure accuracy, precision, recall, and false positive/negative rates
- Refine the model based on evaluation results
5. Deployment and Integration
Hardware and software considerations are critical for successful implementation:
Hardware Components
- Cameras: Industrial-grade cameras with appropriate resolution and frame rates
- Lighting: Consistent, optimized lighting to highlight defects
- Computing Hardware: GPUs for real-time processing of image data
- Rejection Systems: Mechanisms to remove defective packages from the line
Software Architecture
- Integration with production line controls
- User interfaces for monitoring and configuration
- Data storage and management systems
- Connectivity with enterprise systems
6. Continuous Improvement
The most effective systems evolve over time:
- Monitor performance metrics and detection accuracy
- Regularly update models with new data
- Refine detection parameters based on production feedback
- Expand capabilities to address new packaging types or defects
Industry Applications
Image recognition for package inspection benefits numerous industries:
Retail and E-commerce
Ensures products arrive in perfect condition, reducing returns and enhancing customer experience.
Food and Beverage
Detects packaging defects that could compromise food safety or shelf life, such as incomplete seals or damaged containers.
Pharmaceuticals
Verifies critical packaging elements like tamper-evident features, lot numbers, and expiration dates.
Consumer Goods
Maintains brand image through consistent, high-quality packaging presentation.
Logistics and Shipping
Identifies damage that could occur during the distribution process before products reach customers.
Business Benefits
Implementing image recognition for package inspection delivers multiple advantages:
Quality Assurance
- Consistent inspection criteria applied to every package
- Detection of subtle defects invisible to the human eye
- Comprehensive documentation of inspection results
Cost Reduction
- Fewer returns and warranty claims
- Reduced waste from packaging failures
- Lower labor costs for quality control
Operational Efficiency
- Faster production speeds without sacrificing quality
- Reduced line stoppages for manual inspection
- Data-driven insights for process improvement
Brand Protection
- Consistent customer experience
- Reduced risk of social media backlash from packaging failures
- Enhanced reputation for quality and attention to detail
Future Developments
As AI and computer vision technology continue to evolve, we can expect:
- Enhanced Learning Capabilities: Systems that improve accuracy through continuous operation
- Expanded Detection Parameters: More sophisticated analysis of packaging characteristics
- Integration with Predictive Maintenance: Anticipating packaging equipment issues before failures occur
- Augmented Reality Interfaces: Improved visualization of defects and troubleshooting guidance
Conclusion
Package inspection with image recognition represents a significant advancement in manufacturing quality control. By overcoming the limitations of manual inspection, these AI-powered systems help companies ensure consistent packaging quality at production speeds.
For organizations concerned about product protection, regulatory compliance, and brand reputation, automated visual inspection offers a compelling solution that delivers both immediate quality improvements and long-term cost savings. As the technology continues to advance, it will become an increasingly essential component of modern manufacturing and logistics operations.
This article provides a historical perspective on packaging inspection with image recognition. While Visionify now specializes in computer vision solutions for various industries, we recognize the continuing importance of vision-based systems in manufacturing quality control.
Frequently Asked Questions
Find answers to common questions about this topic
Want to learn more?
Discover how our Vision AI safety solutions can transform your workplace safety.
Schedule a DemoSchedule a Meeting
Book a personalized demo with our product specialists to see how our AI safety solutions can work for your business.
Choose a convenient time
Select from available slots in your timezone
30-minute consultation
Brief but comprehensive overview of our solutions
Meet our product experts
Get answers to your specific questions
Related Articles
Subscribe to our newsletter
Get the latest safety insights and updates delivered to your inbox.